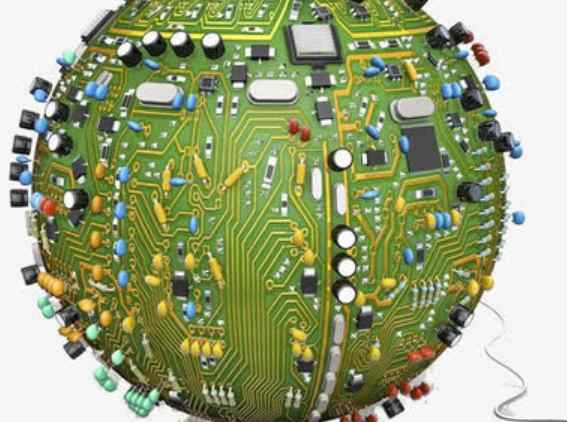
Software anti-jamming has the advantages that hardware anti-jamming cannot replace. In DSP application system, the anti-jamming ability of software should be fully explored, so as to restrain the influence of interference to a minimum. Several effective software anti-jamming methods are given below.
(1) Digital filtering: the noise of the analog input signal can be eliminated by digital filtering. The commonly used digital filtering techniques include median filtering, arithmetic mean filtering and so on.
(2) Set a trap: set up a bootstrap program in the unused program area, when the program is disturbed to this area, the bootstrap program will be forced to capture the program to the specified address, there with a special program to deal with the error program.
(3) Instruction redundancy: two or three bytes of empty operation instruction NOP is inserted after the double-byte instruction and three-byte instruction, which can prevent the program from being automatically brought into the right track when the DSP system is disturbed by the program.
(4) Set watchdog timing: if the out-of-control program enters the "dead cycle", usually the "watchdog" technology is used to make the program out of the "dead cycle". Its principle is to use a timer, it according to the set period to produce a pulse, if do not want to produce this pulse, DSP should be less than the set period of time to clear the timer zero; However, when the DSP program runs away, the timer will not be reset according to the regulations. Therefore, the pulse generated by the timer is used as the DSP reset signal to reset and initialize the DSP again.
Iii. Electromagnetic compatibility design
Electromagnetic compatibility refers to the ability of electronic devices to function properly in complex electromagnetic environments. Emc is designed to enable electronic devices to both suppress various external interference and reduce electromagnetic interference from electronic devices to other electronic devices. In actual PCB board, there is more or less electromagnetic interference phenomenon between adjacent signals, namely crosstalk. The magnitude of crosstalk is related to the distributed capacitance and distributed inductance between circuits. The following measures can be taken to solve this mutual electromagnetic interference between signals:
1. Choose a reasonable wire width
The impulse interference caused by transient current on printed wire is mainly caused by the inductance component of printed wire, and its inductance is proportional to the length of printed wire and inversely proportional to the width. So the use of short and wide wire to suppress interference is advantageous. Clock lead, bus driver signal line often large transient current, its printed wire should be as short as possible. For discrete component circuit, printed wire width in about 1.5mm can meet the requirements; For integrated circuit, printed wire width in 0. 2mm ~ 1. 0mm choice.
2, the use of well pattern network wiring structure.
The specific method is in the PCB board a layer of transverse wiring, next to a layer of longitudinal wiring.
Four, heat dissipation design
In order to facilitate heat dissipation, it is best to install the printed board independently, the board spacing should be greater than 2cm, and pay attention to the layout rules of components on the printed board. In the horizontal direction, the high-power devices are arranged as close as possible to the edge of the printed board, so as to shorten the heat transfer path. In the vertical direction of high-power devices as close as possible to the printed board above the arrangement, so as to reduce its influence on the temperature of other components. Components that are sensitive to temperature should be placed in areas with low temperature as far as possible, and should not be placed directly above devices with large heat output.
In the design of high-speed DSP application system, how to transform perfect design from theory to reality depends on high quality PCB board, DSP circuit working frequency is getting higher and higher, pin more and more dense, interference increase, how to improve the quality of signal is very important. Therefore, whether the performance of the system is good or not is closely related to the quality of the designer's PCB board.
▪ Place a filter capacitor at the connector or within 25mm of the receiving circuit.
(1) Use a short and thick wire to connect to the chassis or the receiving circuit (length less than 5 times the width, preferably less than 3 times the width).
(2) The signal wire and ground wire are first connected to the capacitor and then connected to the receiving circuit.
▪ Make sure the signal line is as short as possible.
▪ When the length of signal cables is greater than 300mm, make sure to lay a ground wire in parallel.
▪ Ensure that the loop area between the signal line and the corresponding loop is as small as possible. For long signal lines, the position of signal lines and ground lines should be changed every few centimeters to reduce the area of the loop.
▪ Drive signals from a central location in the network into multiple receiving circuits.
▪ Ensure that the loop area between the power supply and the ground is as small as possible by placing a high-frequency capacitor close to each power pin on the integrated circuit chip.
▪ Place a high-frequency bypass capacitor within 80mm of each connector.
▪ Where possible, unused areas should be filled with land, connecting all layers of fill at 60mm intervals.
▪ Ensure that the ground is connected at the two opposite end points of any large ground filling area (approximately greater than 25mm x 6mm).
▪ When the length of an opening on the power supply or ground plane exceeds 8mm, connect the two sides of the opening with a narrow wire.
▪ Do not place reset cables, interrupt signal cables, or edge trigger signal cables near the PCB edge.
▪ Connect the mounting holes to the circuit Commons or isolate them.