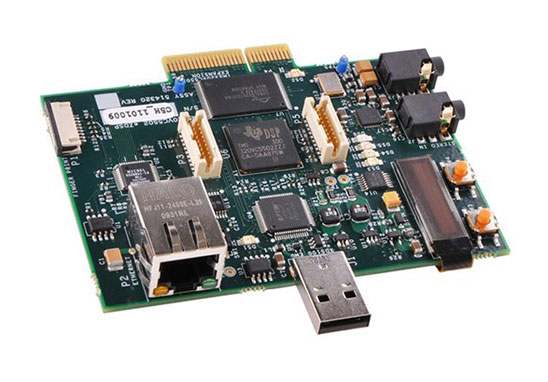
PCB circuit board fault causes are various, only to accurately find the problem point, in order to quickly solve the fault, the next Shenzhen PCBA processing manufacturers for you to introduce the PCB circuit board fault detection method.
PCB circuit board fault detection method
1. Determine the fault location
Once there are signs of a problem, the next step is to track and locate until the defect is identified. Different ways to locate a fault include a visual inspection and a physical inspection using test equipment. Test techniques rely on high-end test equipment or the use of basic tools such as multimeters, thermal imagers, magnifying glasses and oscilloscopes.
2. Testing equipment
Typical equipment includes automated flight detection instruments and automated optical detection (AOI) machines. AOI uses high-resolution cameras to check for a variety of defects, including short circuits, open circuits, missing, incorrect, or misaligned components.
3. Visual and physical detection
Visual inspection identifies defects such as overlap marks, short solder joints, signs of circuit board overheating, and burned components. Some problems are difficult to identify with the naked eye, magnifying glass can help identify some short circuit, welding bridge, open circuit, solder joints and circuit board routing cracks, component offset, etc.
4, special detection components
When low resistance is detected between the component pins, it is best to take the component out of the PCB circuit for specialized testing. If the resistance remains low, then this component is the culprit, otherwise further investigation is needed.
5. Power on the circuit board for detection
Visual inspection is only applicable to the appearance of the circuit board inspection, not to the internal layer of the circuit board inspection. If there are no obvious defects, you will need to power on the board and perform more detailed tests to find out if the board is in good condition.
6, low voltage measurement
The technique involves controlling the current flow through the short circuit and finding the current direction. Since the copper trace on the circuit board also has resistance, the voltage generated through different parts of the copper trace is also different. With a voltmeter, when you measure the voltage between different parts along a short route and find that the voltage value is getting smaller and smaller, you are getting closer and closer to a short circuit.
7, finger sensing circuit board heating area
Because short circuits cause local temperatures to rise, finding areas with heat can help locate the problem spot. However, be careful to use power sources that short circuit copper wires and avoid burns or electric shocks.
8. Repair short/open lines
Once a short or open circuit is identified on the PCB, the next step is isolation. While this is easy to do on the outer surface of the board, it is a challenge for the inner layer. Possible solutions include drilling through holes or cutting appropriate external copper stitches.
2. Which parts of industrial PCBA board are most prone to failure?
Industrial PCBA board due to the complex operating environment, the failure rate is higher than the ordinary circuit board, maintenance to understand the vulnerable parts on the circuit board. So, what parts of the industrial PCBA board are most prone to failure?
Industrial PCBA board is the most prone to failure
l, the design is not reasonable place is the most prone to failure
First of all, the problem of heat dissipation, a lot of circuit board damage is caused by bad heat dissipation design; Secondly, the copper foil wire design of the circuit board is too thin, easy to burn due to the current, so that the motherboard can not work.
2, frequently used places prone to failure
For example, the circuit board of the drive motor, rotating shaft, switching power switch tube, the operation panel of the commonly used keys.
3. Components with heavy load, large power and high working voltage are the most prone to failure
Circuit board power supply, drive circuit, power control devices and other components are generally close to the heat sink, if the protection measures are not enough, the heat dissipation is not good, it is easy to become the first fault.
4, the protection circuit is the most easily damaged
Valuable chips or components on the circuit board are equipped with protective equipment, once the board is abnormal, the first problem is these protective circuits.
5. The interface and line of the inline seat and connector are easy to contact poorly or break the line
Such as board card and slot contact is bad, wire plug and terminal contact is not good, components welding, etc. All belong to this phenomenon.
Shenzhen kingford PCBA processing advantages
1. Highly professional: The company focuses on processing samples and small and medium-sized batches, and promises to deliver the materials within 3-5 working days after confirmation.
2. Professional equipment: The company's equipment is tailored for sample and small and medium-sized batch production of advanced equipment, can stick 0201, BGA spacing 0.3MM, QFN, CSP, CON and other components.
3. Professional technology: 100% of technical backbone workers have more than 5 years of work experience, 85% of front-line operators have more than 3 years of work experience.
4. The company implements the 5S and 6σ concepts in daily operation, so as to ensure that the shipment is checked at least 7 times. If the quantity reaches 100PCS, our company promises to pass AOI optical inspection.
5. The company promises that the straight through rate of welding is more than 99%. If customers find welding defects, the company promises to repair them free of charge.