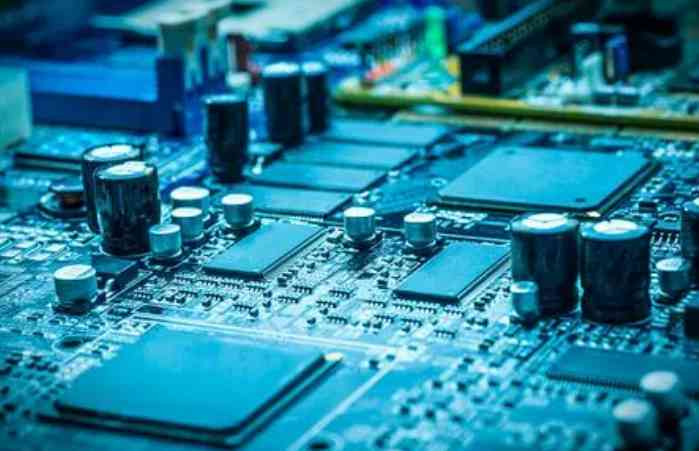
Counterfeit electronic information components pose a major financial risk to industries around the world. These counterfeit parts can affect almost all of our related industries, including social care, automotive, consumer goods, cyber, communications, aerospace and defense.
These components may be neglected during PCBA proofing, which increases the failure rate, scrap rate, and pcb rework rate. This will affect the overall profitability and VAR of SMT proofing mills, with serious consequences for highly reliable applications. Especially in the health care and auto industries. Therefore, the component must pass certain industry-specific tests before SMT proofing and dip plug-in identification of the electronic component.
Manufacturers and suppliers publish a number of specifications and guidelines to establish and maintain product traceability. By adhering to these practices, it is possible to eliminate the use of counterfeit electronic components in the manufacturing process and to ensure that products are genuine electronic components. Hongjie Electronic warranty does not buy counterfeit parts, do not use counterfeit parts, do not recommend unknown parts of these three principles.
What are counterfeit electronic components?
Counterfeit electronic components are counterfeit/counterfeit parts that are misrepresented in terms of origin or quality. Counterfeiting involves passing off low quality parts as high quality parts by changing part numbers, repackaging, or mixing them with better quality parts.
Typical counterfeit parts:
1. The source from which the enterprise is not authorized by the State
2. Manufacture by an unauthorized contractor instead of ocm (original Parts Manufacturer)
3. It violates the original OCM design, type and performance specifications
4. Whether the defective products are sold as new products
5. You have incorrect documents
Why do counterfeit electronic components exist?
First, copy/clone
Cloning is a process in which an enterprise involves the design and manufacture of reverse engineered technical equipment that matches the original equipment in terms of assembly, use and structural development. The products can be manufactured with low - grade equipment. As a result, they will not be able to meet their own reliability requirements. These information device companies are labeled and distributed as OCM components.
Two, scrap
During the manufacturing process, faulty devices are sent to recycling stations to recover valuable metals. Recyclers can prove that equipment was destroyed before it was scrapped and then rejoin the supply chain.
3, misleading
Misrepresentation is a form of fraud involving overproduction or declaring low production.
4. Put the prototype back in the supply chain
And OEM OCMs test, evaluate, and certify a large number of devices. The end-of-life evaluation process includes accelerated testing to determine product performance and reliability. Samples and stolen parts can be resold into the supply chain as brand new products. Most scrapped devices still work after being scrapped, making them prime targets for fraudsters.
5. Deception
High-performance components require rigorously managed testing of Chinese automotive, aerospace, avionics and other enterprise applications. But fraudsters buy lower-spec components for these data applications. Later, they can relabel the parts and resell them at a high price. Printed circuit boards play an important role in the automotive industry.
6, recycling
Many electronic devices contain multiple working devices at the end of their lives. Valuable parts can be recovered from these devices for reuse. Improper component removal may damage the original performance, reliability, and durability. Then a bad supply chain sells the parts.
7. Embedded malware
Counterfeiters usually we will on programmable devices can be reprogrammed, thereby causing potential damage to enterprise product development students. Reprogramming in this way is dangerous, especially in three categories such as military and aerospace plates. This compromises system and user security. Malicious applications can interfere with almost all embedded servers, leading to serious consequences. Usually in the process of tracking research, this will directly lead to different customers' liability and compensation system requirements for hardware manufacturers.
Now the domestic electronic processing industry is very prosperous, Baiqiancheng as a professional patch processing enterprise, naturally, the sooner the better the order, the following is how to effectively reduce the pcba proofing time? This is a very good problem, we want to effectively reduce the time, but also reduce the loss in the process of processing, the following hundreds of achievements to explain to you in detail!
First of all, in the electronics processing industry, there are always rush orders for something. In order to effectively reduce PCBA proofing, it is not a waste of time to do something other than proofing first. For example, when carefully reading PCBA proofing documents and determining the overall proofing requirements, it is necessary to prepare the required materials and arrange the proofing personnel in advance. If two shifts are required, staff attendance and shifts should also be assigned to ensure that all preparations other than technical work are completed.
Secondly, the planning of pcba proofing scheme should be more scientific and standardized. Usually, pcba proofing takes five days to half a month, and the reason why there are many enterprises with different development times is probably due to the lack of standardization in the design research scheme, which makes the manufacturer take a detour in the production. Therefore, the design teaching program should be standardized, such as how much heat dissipation hole should be reserved for the circuit board, and where to mark the location of silk screen printing, etc., there may be only a kind of parameters written in the design activity planning, but can get effective methods to reduce the pcba proofing time.
Third, it is also important to control the number of proofing personnel. If pcba proofing is too large in the initial scheme, it will lead to an increase in cost, and try to do as much pcba proofing as possible, there is a possibility of burning cardboard in the performance test.
The above points are based on the online data and the experience of their own enterprises to reduce the time of pcba proofing methods, in addition to the pcba proofing efficiency and technical experience and other factors, so as a processing enterprise should be improved in technology.