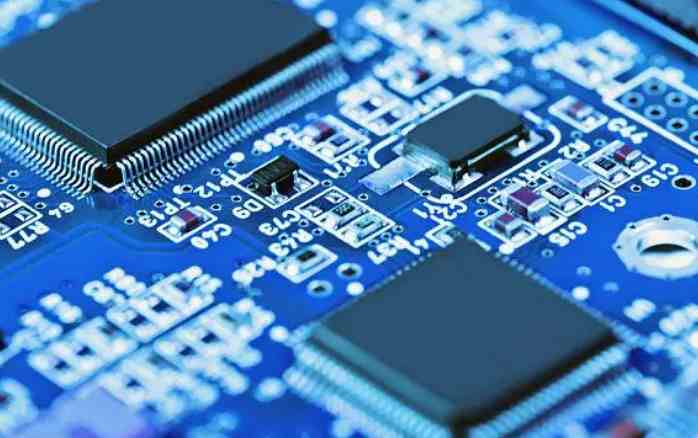
Climate change and society's growing sensitivity to environmental issues require the development of technological solutions for fossil fuel-powered vehicles. Regulatory requirements to phase out emissions call for the design of smaller internal combustion engines with higher engine speeds and the ability to run on less dense fuel mixtures.
These technical requirements inevitably have an impact on the operating conditions of the insulated-gate bipolar transistors (IGBTs) used in engine ignition and control systems: these devices must acquire higher clamp voltages and switching frequencies, with the accompanying heat dissipation capability. Here, we consider the influence of different cooling PCB pads on IGBT thermal performance under different working conditions.
IGBT and thermal performance
The working junction temperature (Tvj(op)) is the basis of device operation and should be regarded as a practical value. When the junction temperature of a normal switch is calculated using conduction losses, switching losses, and thermal impedance, the junction temperature must always remain between the specified minimum and maximum values of Tvj(op), even under overload conditions.
In fact, the temperature of the joint must be kept below Tvj(op) max until the last switching event. Transient temperature increases caused by switching losses in switching events can be ignored if the device is in use within its safe working area and Tvj does not exceed Tvj max. Thermal management and cooling solutions are increasingly receiving attention from IGBTs because of increased heat loss in their applications. Heat loss is divided into two categories: conduction loss and switching loss.
Conduction loss occurs during the switching state voltage drop through the IGBT and depends on the current conducted. Switching power losses occur during the on and off phases of IGBTs and depend on current, operating period, switching voltage, and switching frequency.
Evolution of the internal combustion engine
New emissions regulations require significant changes to the design of internal combustion engines, including spark ignition (SI) as well as more efficient compression ignition (CI) types.
To meet the demand for more efficient, less polluting engines, automakers are following three basic strategies:
Engine sizing and hybrid power. These technologies adjust the size of the engine according to the class of vehicle, maintaining the same power value. As a result, higher revolutions are obtained, which in turn involve a higher frequency of injection system switching and a higher operating temperature.
Dilution of mixture. This method requires the use of a wider gap (necessary for proper heat dissipation) and a higher voltage to trigger the spark plug. Therefore, it is necessary to use IGBT with higher operating voltage.
Direct injection in compression stroke. This technique results in the formation of areas rich in combustible mixture near the spark plug, thus maintaining a poor mixture overall. However, high local and time variations occurring around the spark plug can jeopardize the injection system, which is designed to cover more space and longer ignition cycles. This solution requires IGBT with very high breakdown voltage.
Therefore, IGBTs used in ignition systems must be able to withstand high currents and have high clamp voltages under operating conditions that inevitably generate more heat.
In particular, IGBTs with low collector-emitter on-voltage (Vce(ON)) values are required to reduce power losses and junction temperatures.
Test program
To verify the effect of low Vce(ON) values on temperature and to assess the effect on thermal performance of IGBTs with different PCB pads, a simplified test stand can be used. Here, the inductance simulates the electrical characteristics of commercially available ignition coils.
By varying the switching frequency and residence time, the device under test (DUT) is placed in the position corresponding to the different types of pads made on the PCB and kept running long enough to achieve a stable temperature.
The tests were conducted using PCBS with five types of pads, each with its own heat transfer. To be more precise, the test uses:
A PAD in which there is no heat conduction path from the IGBT collector to the PCB (PAD 0);
PAD (PAD 1) with the same area as IGBT package;
A PAD with the same area as IGBT (PAD 2); and
Two pads with a recommended PAD area for a specific device, no pads (PAD 3) and heat diffusion from top to bottom of the PCB (Pad 4).
To quantify the thermal performance improvement due to lower Vce(ON), we compared NGD8201A (Vce(ON) typical values using Littelfuse DPAK packaging. 1.35V) obtained measurement results and using commercial ignition IGBT (Vce (ON). 1.5V, labeled Ignition IGBT A in Figure 3).
The results shown in the figure show that a slightly higher Vce(ON) results in a slightly higher steady-state temperature, regardless of the type of PCB pad used. As expected, the effect was more pronounced at high switching frequencies.
Figure 4 shows the effect of using different PCB pads. The results show that higher switching frequency leads to higher steady-state temperature. More interesting is that the PCB pad reduces the measured temperature, especially at high switching frequencies.
Steady-state enclosure temperature diagrams of PCB PAD2 and PAD3 at different frequencies indicate that the two pads have the same average heat dissipation capacity. The results correlate with the ignition platform, where size is a key factor.