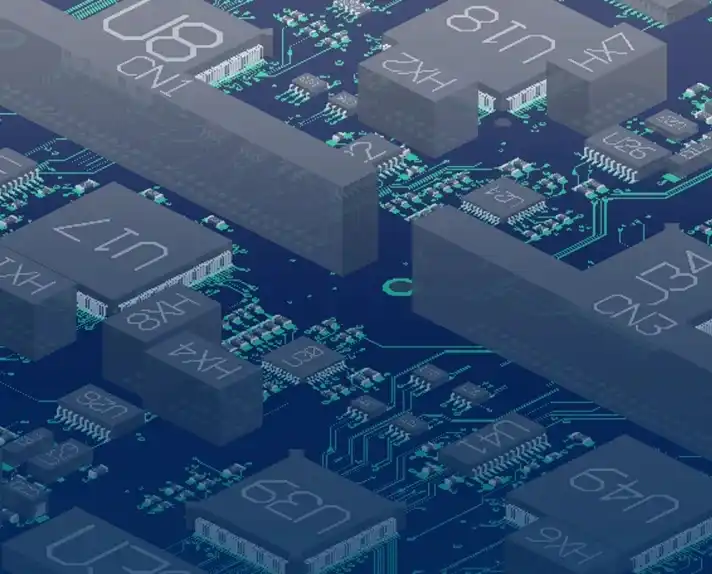
Design for Manufacturing and Assembly (DfMA) is a design methodology that focuses on ease of manufacturing and efficiency in assembly. By simplifying the design of a product, it can be manufactured and assembled more efficiently in the shortest time and at a lower cost.
DfMA combines two approaches - Design for Manufacturing (DFM) and Design for Assembly (DFA): Design for Manufacturing (DFM)
DFM involves designing for ease of manufacture of product components. It focuses on selecting the most cost-effective materials and processes for production and minimizing the complexity of manufacturing operations.
Design for Assembly (DFA) DFA deals with the design of products for easy assembly. It focuses on reducing product assembly costs and minimizing the number of assembly operations.
Both DFM and DFA seek to reduce material, overhead and labor costs.
The main principles of the DfMA are:
Minimize component count: This reduces assembly and ordering costs, reduces work in process, and simplifies automation.
Design for easy part fabrication: Simplify part geometry and avoid unnecessary features.
Part Tolerances: Parts should be designed within the capabilities of the process.
Clarity: Components should be designed so that they can only be assembled in one way.
Minimize the use of flexible parts: parts made of rubber, gaskets, cables, etc. should be limited as handling and assembly are often more difficult.
Design for easy assembly: For example, use a snap fit and adhesive bonding instead of threaded fasteners such as nuts and bolts. Where possible, products should be designed with one basic component to allow for quick and accurate positioning of other components.
Eliminate or reduce required tweaks: Designing tweaks in the product means more opportunities for non-adjustments.
Some of the key benefits of DfMA include:
speed
One of the main advantages of DfMA in construction is the significant reduction of on-site projects through the use of prefabricated elements.
Reduce assembly costs
By using fewer parts, reducing labor required, and reducing the number of unique parts, DfMA can significantly reduce assembly costs.
Higher quality and sustainability
A highly automated approach improves quality and efficiency at every stage.
Less waste may be generated during the construction phase, increasing the efficiency of on-site logistics and reducing the movement of vehicles to bring materials to the site.
shorter assembly time
DFMA reduces assembly time by utilizing standard assembly practices such as vertical assembly and self-aligning parts.DFMA also ensures that the transition from the design phase to the production phase is as smooth and fast as possible.
Improve reliability
DfMA increases reliability by reducing the number of parts, thereby reducing the chance of failure.
Safety
By removing construction activities from the site and placing them in a controlled factory environment, there may be significant positive impacts on safety