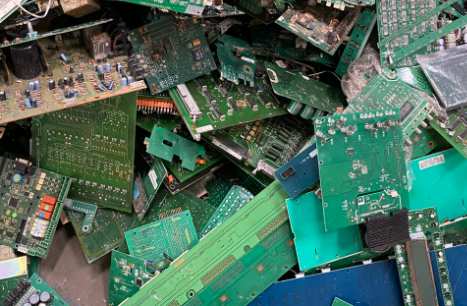
PCB multilayers rarely have odd layers, why are they all even layers
PCB board has double-sided PCB, four-layer PCB, six-layer PCB, eight-layer PCB, etc. At present, there are more than 100 layers of PCB, then why do people have "PCB multilayer board why are even layers?" What about this question? Relatively speaking, even layer PCB does have more than odd layer PCB.
PCB board has double-sided PCB, four-layer PCB, six-layer PCB, eight-layer PCB, etc. At present, there are more than 100 layers of PCB, then why do people have "PCB multilayer board why are even layers?" What about this question? Relatively speaking, even layer PCB does have more than odd layer PCB.
1, the balance structure to avoid bending
The reason for not designing PCBS with odd layers is that odd layers are easy to bend. When the PCB is cooled after the multilayer circuit bonding process, the different lamination tension between the core structure and the foil structure can cause the PCB to bend when cooled. As the board thickness increases, the risk of bending becomes greater for composite PCBS with two different structures. The key to eliminate circuit board bending is to use balanced layering. Although PCBS with a certain degree of bending meet the specification requirements, subsequent processing efficiency will be reduced, resulting in increased costs. Because assembly requires special equipment and technology, the accuracy of component placement is reduced, so the quality will be damaged.
To put it in a more understandable way: In PCB process, four-layer board is easier to control than three-layer board, mainly in the aspect of symmetry, the warpage degree of four-layer board can be controlled below 0.7% (IPC600 standard), but when the size of three-layer board is large, the warpage degree will exceed this standard, which will affect the reliability of SMT and the whole product, so generally designers do not design odd layer board , even if the odd layer to achieve the function, will also be designed as false even layer, that is, 5 layers design into 6 layers,7 layers design into 8 layers.
2. Low cost
Because there is one less layer of medium and coating foil, the cost of odd-numbered PCB board raw materials is slightly lower than that of even-numbered PCB board. But the processing cost of odd layer PCB is obviously higher than that of even layer PCB. The inner layer has the same processing cost, but the foil/core structure significantly increases the processing cost of the outer layer.
Odd layer PCB needs to add non - standard laminated core layer bonding technology on the basis of nuclear structure technology. Compared with the nuclear structure, the production efficiency of the plant adding foil outside the nuclear structure will decrease. Prior to laminating, the outer core requires additional processing, which increases the risk of scratches and etching errors on the outer layer.
For the above reasons,PCB multilayer boards are mostly designed with even layers, and odd layers are less.
So how to reduce the cost and balance the stacking of odd-layer PCBS?
What if there are an odd number of PCBS in the design? The following methods can be used to balance layering, reduce PCB production costs and avoid PCB bending.
1) Add an additional power layer. This method can be used if the PCB is designed with odd power layers and even signal layers. An easy way to do this is to add a layer in the middle of the stack without changing the other Settings. Route an odd number of PCB layers first, then duplicate layers in the middle and label the remaining layers. This is the same electrical property as the coating of thickened layers.
2) A signal layer and use. This method can be used if the PCB is designed with even power layers and odd signal layers. The additional layer does not increase the cost, but can shorten the lead time and improve PCB quality.
3) Add a blank signal layer near the PCB stack. This method reduces layering unbalance and improves PCB quality. The odd-numbered layers are routed, and a blank signal layer is added to mark the remaining layers. In microwave circuits and mixed media (media with different permittivity) circuit types are used.
4 For conventional FR4 materials, if the single core plate does not have a blind buried hole structure, it is not allowed to use the direct pressing of the core plate for lamination design. Instead, PP+ inner core plate should be used for design: e.g
5 Negative plating process must be adopted for the outer layer of the plate in the second-order HDI process. (i.e., the outer plating adopts negative plating, the outer graphics adopts negative process, and the inner etching line is used to process the outer line)
6. Refer to HDI and Mechanical Blind Buried Hole Prelaying Ratio for the provisions on the prelaying ratio of the inner core plate of the laminated plate with multiple times.
7 Laser drilling capacity:
8. For PP+ inner core laminated inner panels, the panels have blind hole design and surface copper thickness requirements to complete 1OZ copper thickness with 12um copper foil or 12um copper foil RCC, after negative plating to meet the requirements;
9. The inner layer is required to complete the RCC of 12um copper foil or 12um copper foil for HOZ copper thickness. The inner layer electroplating hole process is followed by the etching process of negative film.
10. There are no blind holes in the plates. Only the plates with copper thickness requirements can be processed directly with the copper foil thickness required by the customer, without the process of copper sinking and electroplating.
11. For the core plate pressed directly, such as the plate needs to be electroplated, the inner core plate should be made of yin-yang copper structure as far as possible.
12. For the compensation of the outer layer of multiple pressed plates, please refer to the Supplementary Regulations for the Compensation of the Outer Circuit of Blind Plate.
13. For all types of hole plating process (through hole, blind hole, buried hole, etc.), regardless of plate thickness and aperture, the size of hole plating film pad is unified as: diameter of drill tool +3mil (that is, increase 1.5mil on one side).
14. Second-order HDI plates shall not contain outer surface treatment of full plate gold plating (water gold), metallized edge coating, metallized slot holes.