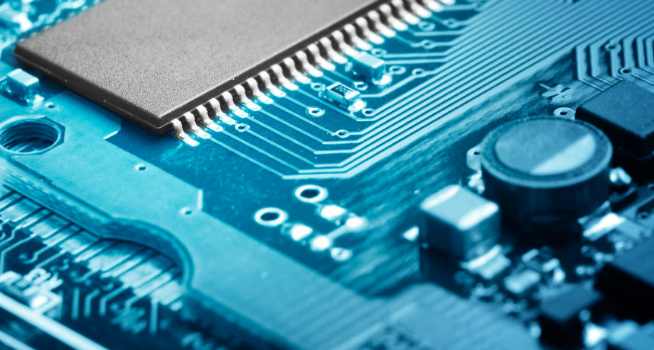
Even a sweet spot tool like Sherlock needs to be integrated into a user-friendly, highly productive design flow in order to deliver its full value in a customer's design environment. Only with smooth data exchange using upstream and downstream tools can engineers quickly and efficiently leverage Sherlock's diverse capabilities. This design flow integration minimizes scripting, data format conversion, and error-prone and time-consuming manual intervention. Sherlock interacts with ANSYS's Icepak and ANSYS Mechanical to combine these tools into a highly productive and highly reliable design process to achieve the goal of "zero defects" required by a growing number of applications.
Ansys Icepak provides powerful electronic cooling solutions for thermal and fluid flow analysis of integrated circuits (ics), packages, printed circuit boards (PCBS) and electronic components using the industry-leading Ansys Fluent Computational Fluid dynamics (CFD) solver. Ansys Icepak CFD solver uses the Ansys Electronics Desktop (AEDT) graphical user interface (GUI).
This provides engineers with a CAD-centric solution that enables them to manage thermal issues within the same unified framework as Ansys HFSS, Ansys Maxwell, and Ansys Q3D Extractor with an easy-to-use ribbon interface. Electrical and mechanical engineers in this work environment enjoy fully automated design processes that seamlessly couple HFSS, Maxwell, and Q3D Extractor to Icepak for steady-state or transient thermal analysis.
Engineers can rely on Icepak to provide integrated electronic cooling solutions for a variety of electronic applications from individual ics to packages and PCB boards to computer casings and entire data centers. Icepak solver performs conduction, convection, and radiation conjugate heat transfer analysis. It has many advanced features, capable of simulating laminar and turbulent flow as well as multi-type analysis, including radiation and convection. Icepak offers a huge library of fans, radiators and materials that provide solutions to everyday electronic cooling problems.
5G connectivity is a coming technological revolution. This ubiquitous, super-fast computing network will connect billions of data-driven devices. This will fuel economic expansion across industries, lead to new products and services, and change the way we've always known life. However, before 5G can fully live up to its promise and meet its quality of service (QoS) targets, wireless system designers and engineers will have to overcome no small challenge. The Ansys 5G Simulation solution enables these people to simplify the complexity of device, network and data center design.
Ansys 5G Simulation Solutions provide electromagnetic, semiconductor, electronic cooling and structural analysis tools to accurately simulate 5G radio and related technologies. The multi-solution platform leverages high-performance computing that can be deployed across the enterprise, making collaboration between designers and engineering experts more efficient.
Phased array design flow in ANSYS HFSS. ANSYS HFSS is a 3D high-frequency electromagnetic (EM) tool that can be used to design and simulate a wide range of high-frequency (HF) electronics, such as antennas, antenna arrays, RF and microwave components, resonators, filters, and other HF electronic components. The phased array design process in HFSS begins with a single unit prototype and optimizes antenna design parameters through the Design of Experiments (DoE) method. Then, the full array is synthesized from the element so that the performance of the full array can be simulated and optimized in ANSYS HFSS. Then, the hybrid ANSYS HFSS SBR+ ray-tracking solver is used to model and simulate the installed antenna and its interaction with the environment.
High Tg means high heat resistance. With the rapid development of the electronic industry, especially the electronic products represented by computers, towards the development of high function and high multilayer, the higher heat resistance of PCB substrate material is needed as an important guarantee. With the emergence and development of high density installation technology represented by SMT and CMT, PCB is increasingly dependent on the support of high heat resistance of substrate in terms of small aperture, fine line and thin shape.
Therefore, the difference between general FR-4 and high Tg FR-4 is that the mechanical strength, dimensional stability, adhesion, water absorption, thermal decomposition, thermal expansion and other conditions of the material are different in the hot state, especially after moisture absorption. High Tg products are obviously better than ordinary PCB substrate materials.
Among them, the expansion of the core plate that makes the inner pattern is different due to the difference between the pattern distribution and the thickness of the core plate or the material characteristics. When the pattern distribution is different from the thickness of the core plate or the material characteristics, the pattern distribution is uniform and the material type is consistent, there will be no deformation. When the PCB lamination structure is asymmetrical or the pattern distribution is not uniform, the CTE difference of different core boards will be large, resulting in deformation in the process of pressing. The deformation mechanism can be explained by the following principles.
It is assumed that two core plates with significantly different Ctes are pressed together by semi-curing sheet. The CTE of core plate A is 1.5x10-5/℃, and the length of core plates is 1000mm. In the pressing process, the semi-cured sheet as a bonding sheet is glued together by three stages: softening, flowing and filling pattern and curing.
Is the dynamic adhesive base curve of ordinary FR-4 resin at different heating rates. In general, the material starts to flow at about 90℃ and cross-linked curing begins when it reaches the TG point. Before curing, the semi-cured sheet is in a free state, and the core plate and copper foil are in a state of free expansion after being heated, and their deformation can be measured by their respective Ctes and temperature changes.