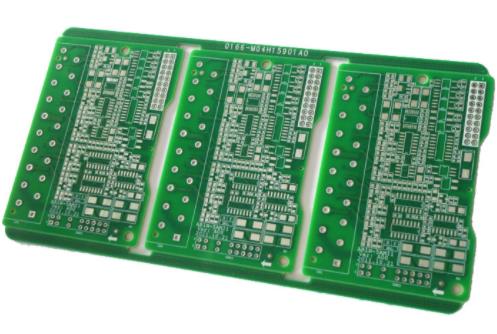
Methods and Characteristics of Circuit Board Profile Processing
Circuit board manufacturing, circuit board design and PCBA processing manufacturers explain the methods and characteristics of circuit board contour processing
The contour processing of circuit boards is very important for boards with strict tolerance requirements. It is an important condition to ensure correct electrical and mechanical installation
The circuit board contour processing can select different processing technologies according to the geometric shape of the circuit board contour, processing quantity, layers and materials. The common methods are as follows:
1: Shearing
This processing method is carried out on a shearing machine. Shear processing can be used for blanking, and also for contour processing of plates with low tolerance requirements. When using the shearing machine to process the contour of the circuit board, the border line is taken as the processing benchmark. The shearing process can only process the linear contour, and the irregular part can be processed by the punch and milling machine. This type of processing technology is usually used for circuit boards with many varieties, few quantities and low requirements for overall dimensions. Its disadvantage is that the precision is relatively poor, and sometimes sandpaper is used to polish to meet the requirements for overall dimensions.
Shearing machine processing is also divided into cutting on flat edge shearing machine and cutting on inclined edge shearing machine.
① Shearing on flat blade shears
The flat blade shearing machine has two cutting edges, the lower blade is fixed on the workbench of the shearing machine, and the upper blade is fixed on the sliding block of the shearing machine. The slider moves up and down under the drive of the crank linkage mechanism. The sheared sheet is placed on the workbench between the upper and lower knives and separated by the movement of the upper scissors. It is called because the upper and lower scissors are parallel to each other. This type of shearing machine is characterized by that: the upper scissors contact with the sheared sheet in the whole width direction at the same time, and the whole width of the sheet is cut at the same time, so the required shearing force is relatively large.
Flat blade shears are suitable for cutting sheet materials with small width and large thickness. They can only cut materials along a straight line.
② Cutting on inclined edge shears
The shearing principle of the inclined blade shearing machine is the same as that of the flat blade shearing machine, except that the upper blade is inclined and forms an included angle with the lower blade. Compared with the flat blade shearing machine, when shearing, it is not along the entire width direction of the sheet, but only a part of the material is sheared. With the decline of the cutting edge, the two parts of the sheet are gradually separated along the width direction continuously. Therefore, in the shearing process, the force required is relatively small, and its value is approximately a constant. As the falling of the upper shear blade bends the separated sheet downward and deforms, the cut sheet is bent and twisted. Especially when cutting the copper clad foil substrate material, it is easy to produce transverse cracks. Therefore, this material needs to be heated when blanking with this equipment.
The thicker the cutting material is, the greater the gap and tilt angle between the upper and lower blades are. On the contrary, the smaller the gap and tilt angle are. The shearer should be equipped with a baffle and a positioning ruler to adjust the size of the sheared plate.
③ Thin substrate material shearing
Special attention shall be paid to the blanking of thin base materials. As the substrate material is thin and soft, the slightly careless blanking will lead to tearing. Therefore, a special cutting system for thin base materials is required to ensure the surface quality and size requirements of soft and thin materials.
2: Punch processing
The clearance between the punch and the die shall be reasonably designed according to the material thickness and overall dimensions of the processed circuit board, so as to obtain the overall dimensions and geometric dimensions with a certain accuracy, and the typical outline blanking die structure.
If the one-time punching blanking die is used, the compound die structure can be used. The stamping process has high production efficiency, good consistency of processing circuit boards, and is suitable for mass production.
3: Milling machine processing
This processing method is flexible and suitable for automatic production. As the milling cutter is cylindrical, the excessive arc at the corner must be allowed to be greater than or equal to the radius of the small milling cutter when designing the circuit board shape and the special-shaped hole. CNC milling machine can process the shape of circuit board with high processing accuracy, and can process boards of various shapes and sizes. NC milling is applicable to the milling of circuit boards with complex shapes and high precision requirements in mass production. The movement of the worktable or spindle of the NC milling machine is automatically controlled by the program. The operator only needs to program according to the overall dimensions and load and unload the circuit board on the NC table. PCB manufacturers, PCB designers and PCBA manufacturers will explain the methods and characteristics of PCB shape processing.