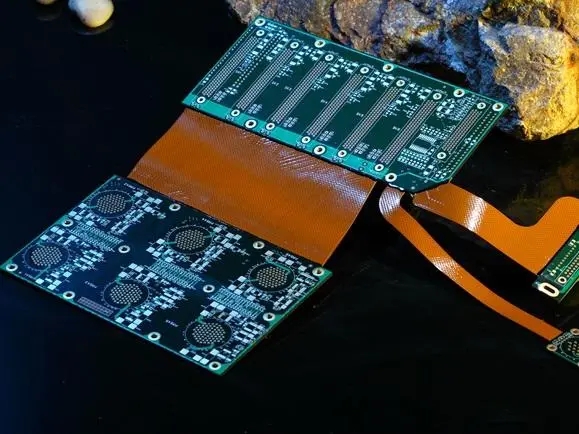
Pcb electronic factory: small edition introduces the principle of horizontal electroplating
Introduction to Horizontal Electroplating Principle
The method and principle of horizontal electroplating and vertical electroplating are the same, both of which must have negative and positive poles. After being energized, electrode reaction will be generated to ionize the main components of the electrolyte, so that the charged positive ions will move to the negative phase of the electrode reaction zone; The charged negative ions move to the positive phase of the electrode reaction zone, resulting in metal deposit coating and gas emission.
Because the process of metal deposition in the cathode is divided into three steps: that is, the hydrated ions of metal diffuse to the cathode; The second step is that the metal hydrated ions are gradually dehydrated and adsorbed on the cathode surface when passing through the double electric layer; The third step is that the metal ions adsorbed on the cathode surface receive electrons and enter the metal lattice. From the actual observation, the situation of the operation tank is an unobservable heterogeneous electron transfer reaction between the solid electrode and the interface of the liquid electroplating solution. Its structure can be explained by the double electric layer principle in electroplating theory. When the electrode is a cathode and in a polarized state, the cations surrounded by water molecules and with positive charges are orderly arranged near the cathode due to the electrostatic force. The design phase surface formed by the center point of the cations closest to the cathode is called Helmholtz outer layer, which is about 1-10 nanometers away from the electrode. However, due to the total electric quantity of positive charge carried by the outer cation of Helmholtz, its positive charge is not enough to neutralize the negative charge on the cathode. The solution far from the cathode is affected by convection, and the concentration of cations in the solution layer is higher than that of anions. This layer is smaller than the Helmholtz outer layer due to the electrostatic force effect, and is also affected by the thermal movement. The cation arrangement is not as tight and neat as the Helmholtz outer layer. This layer is called the diffusion layer. The thickness of the diffusion layer is inversely proportional to the flow rate of the bath. That is, the faster the flow rate of the plating solution is, the thinner the diffusion layer is, and the thicker it is. Generally, the thickness of the diffusion layer is about 5-50 microns. It is farther away from the cathode, and the bath layer reached by convection is called the main bath. Because the convection generated by the solution will affect the uniformity of the bath concentration. Copper ions in the diffusion layer are transported to the outer layer of Helmholtz by diffusion and ion migration of the plating solution. However, copper ions in the main bath are transported to the cathode surface by convection and ion migration. In the horizontal electroplating process, the copper ions in the plating solution are transported to the vicinity of the cathode by three ways to form a double electric layer.
Convection of plating solution is generated by mechanical stirring and pump stirring inside and outside, swinging or rotating of electrode itself, and flow of plating solution caused by temperature difference. At the place closer to the surface of the solid electrode, the flow of the electroplating solution becomes slower and slower due to the influence of its friction resistance. At this time, the convection rate on the surface of the solid electrode is zero.
The velocity gradient layer formed from the electrode surface to the convection plating solution is called the flow interface layer. The thickness of the flow interface layer is about ten times that of the diffusion layer, so the transport of particles in the diffusion layer is almost not affected by convection.
Under the action of electric field, ions in electroplating solution are subject to electrostatic force, which causes ion transport, which is called ion migration. The migration rate is expressed by the formula: u=zeoE/6 π r η Yes. Where u is the ion migration rate, z is the charge number of ions, eo is the charge amount of one electron (i.e. 1.61019C), E is the potential, r is the radius of hydrated ions η Is the viscosity of the electroplating solution. According to the calculation of the equation, the greater the drop of potential E, the smaller the viscosity of the electroplating solution, and the faster the rate of ion migration.
According to the electrodeposition theory, when electroplating, the printed circuit board on the cathode is a non ideal polarized electrode. The copper ions adsorbed on the cathode surface obtain electrons and are reduced to copper atoms, thus reducing the concentration of copper ions near the cathode. Therefore, a copper ion concentration gradient will be formed near the cathode. The bath with a lower concentration of copper ions than the main bath is the diffusion layer of the bath. The copper ion concentration in the main bath is high, which will diffuse to the place near the cathode where the copper ion concentration is low, and constantly supplement the cathode area.
The printed circuit board is similar to a planar cathode, and the relationship between the current and the thickness of the diffusion layer is the COTTRELL equation: where I is the current, z is the charge number of copper ions, F is the Faraday constant, A is the cathode surface area, and D is the diffusion coefficient of copper ions (D=KT/6 π r η), Cb is the concentration of copper ions in the main bath, Co is the concentration of copper ions on the cathode surface, D is the thickness of the diffusion layer, K is the Boltzmann constant (K=R/N), T is the temperature, r is the radius of copper hydrate ions η Is the viscosity of the electroplating solution. When the copper ion concentration on the cathode surface is zero, the current is called the limiting diffusion current ii:
It can be seen from the above formula that the limit diffusion current depends on the concentration of copper ions in the main bath, the diffusion coefficient of copper ions and the thickness of the diffusion layer. When the concentration of copper ions in the main bath is high, the diffusion coefficient of copper ions is large, and the thickness of the diffusion layer is thin, the limit diffusion current is larger. According to the above formula, in order to reach a higher limit current value, appropriate process measures must be taken, that is, heating process method. Because the diffusion coefficient increases with increasing temperature, increasing the convection rate can make it become eddy current and obtain a thin and uniform diffusion layer. From the above theoretical analysis, increasing the concentration of copper ions in the main plating solution, increasing the temperature of the plating solution, and speeding up the convection rate can increase the limiting diffusion current, so as to accelerate the electroplating rate. Horizontal electroplating is based on the eddy current formed by accelerating the convection speed of the plating solution, which can effectively reduce the thickness of the diffusion layer to about 10 microns. Therefore, when the horizontal electroplating system is used for electroplating, the current density can be as high as 8A/dm2.
The key of PCB electroplating is how to ensure the uniformity of copper layer thickness on both sides of the substrate and the inner wall of the through hole. To obtain the uniformity of coating thickness, it is necessary to ensure that the flow rate of plating solution on both sides of the PCB and in the through-hole is fast and consistent, so as to obtain a thin and uniform diffusion layer. To achieve a thin and uniform diffusion layer.
As far as the structure of the current horizontal electroplating system is concerned, although there are many nozzles installed in the system, the plating solution can be sprayed to the printed circuit board rapidly and vertically, so as to accelerate the flow speed of the plating solution in the through hole, resulting in a fast flow rate of the plating solution, forming eddy currents on the upper and lower parts of the substrate and in the through hole, so that the diffusion layer is reduced and uniform. However, when the plating solution suddenly flows into the narrow through-hole, the plating solution at the inlet of the through-hole will also have a reverse reflux phenomenon. In addition, the influence of the primary current distribution will often lead to the electroplating of the hole at the inlet. Due to the tip effect, the copper layer is too thick, and the inner wall of the through-hole forms a dog bone shaped copper coating.
According to the flow state of the plating solution in the through-hole, that is, the size of eddy current and reflux, and the state analysis of the quality of the conductive plating through-hole, the control parameters can only be determined by the process test method to achieve the uniformity of the plating thickness of the printed circuit board. Since the size of eddy current and reflux is still unknown through theoretical calculation, only the measured process method is used. From the measured results, it can be seen that to control the uniformity of the thickness of the copper plating layer on the through-hole, it is necessary to adjust the controllable process parameters according to the aspect ratio of the through-hole of the printed circuit board, and even select a copper plating solution with high dispersion capacity, add appropriate additives and improve the power supply method, that is, use reverse pulse current for electroplating to obtain a copper coating with high distribution capacity.
In particular, with the increase of the number of micro blind holes in the laminate, it is not only necessary to use the horizontal electroplating system for electroplating, but also to use ultrasonic vibration to promote the replacement and circulation of the plating solution in the micro blind holes, and then improve the power supply mode to adjust the controllable parameters using the reverse pulse current and the actual test data, which can achieve satisfactory results.
PCB manufacturers, PCB designers and PCBA processors will explain the principle of horizontal electroplating of PCB.