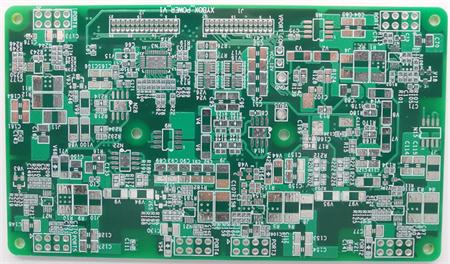
1 Surface tension
The cohesion of tin lead solder is even greater than that of water, making the solder a sphere to minimize its surface area (under the same volume, the sphere has the smallest surface area compared with other geometric shapes to meet the requirements of the lowest energy state). The function of the flux is similar to that of the cleaner on the metal plate coated with grease. In addition, the surface tension is also highly dependent on the cleanliness and temperature of the surface. Only when the adhesion energy is far greater than the surface energy (cohesion) can ideal tin adhesion occur.
2 Production of metal alloy compounds
The intermetallic bond between copper and tin forms grains. The shape and size of grains depend on the duration and strength of the temperature during welding. Less heat during welding can form fine crystalline structure, forming excellent welding points with the best strength. If the reaction time of patch processing is too long, whether it is due to too long welding time, too high temperature or both, it will lead to rough crystalline structure, which is sandy and brittle, with low shear strength.
3 Tin dipping angle
When the eutectic point temperature of solder is about 35 ℃ higher than that of solder, a meniscus is formed when a drop of solder is placed on the hot surface coated with flux. To some extent, the ability of metal surface to stick tin can be evaluated by the shape of the meniscus. If the solder meniscus has an obvious undercut, such as water drops on a greased metal plate, or even tends to be spherical, the metal is not weldable. Only when the meniscus is stretched to a small angle of less than 30 ° can it have good weldability.
4 Tinning
When the hot liquid solder dissolves and penetrates into the metal surface to be welded, it is called metal tin or metal tin. The molecules of the mixture of soldering tin and copper form a new kind of alloy that is partly copper and partly solder. This solvent action is called dipping tin, which forms intermolecular bonds between various parts to form a metal alloy compound. The formation of good intermolecular bond is the core of welding process, which determines the strength and quality of welding points. Only the copper surface is free from pollution, and no oxide film formed due to exposure to air can be stained with tin, and the soldering tin and working surface need to reach appropriate temperature.
5 Copper is used as the metal substrate, and tin lead is used as the solder alloy. Lead and copper will not form any metal alloy complexes. However, tin can penetrate into copper. The intermolecular bond between tin and copper forms metal alloy complexes Cu3Sn and Cu6Sn5 at the junction surface between solder and metal.
Metal alloy layer (n-phase+ ε Phase) must be very thin. In laser welding, the order of magnitude of the thickness of the metal alloy layer is 0.1mm. In wave soldering and manual soldering of PCB boards, the thickness of the metal bonds at the excellent welding points mostly exceeds 0.5 μ m 。 As the shear strength of the welding point decreases with the increase of the thickness of the metal alloy layer, it is often tried to keep the thickness of the metal alloy layer at 1 μ M below, which can be achieved by making the welding time as short as possible.
The thickness of the metal alloy eutectic layer depends on the temperature and time of forming the welding point. Ideally, the welding should be completed in about 220't 2s. Under this condition, the chemical diffusion reaction of copper and tin will produce an appropriate amount of metal alloy bonding materials Cu3Sn and Cu6Sn5 with a thickness of about 0.5 μ m 。 Inadequate intermetallic bonds are commonly found in cold welding points or welding points that have not been raised to an appropriate temperature during welding, which may result in the cutting off of the welding surface. On the contrary, too thick metal alloy layer is commonly used in welding points that are overheated or welded for too long, which will lead to very weak tensile strength of welding points.
The above is about the method of improving the PCB circuit board soldering to cause false soldering and false soldering