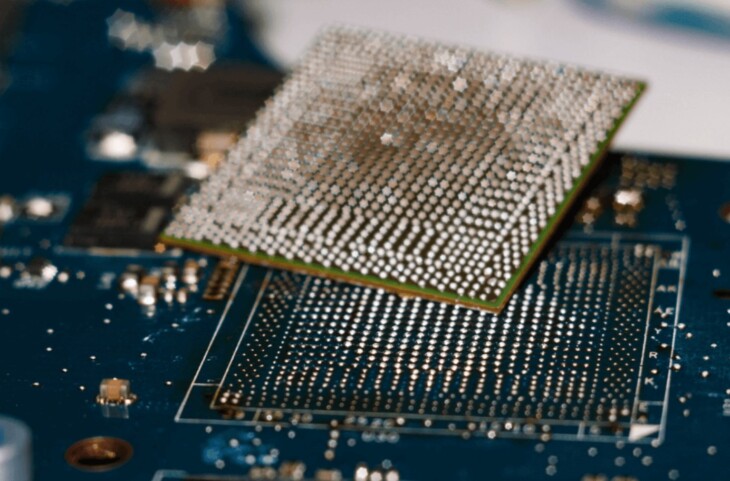
1.Since the temperature of the solder pins of the chip is always higher than the temperature of the overall circuit board, the unevenness of
infrared heating at the bottom will cause the deformation of the circuit board, causing the solder joints of other components on the circuit
board to be subject to great deformation stress, resulting in the entire The reliability of circuit boards after single-chip rework is unpredictable.
For large-size circuit boards, multi-layer boards, and circuit boards with large-area ground wiring, it is almost impossible to reliably solder with
equipment using infrared heating technology. In addition, because infrared heating does not use nozzles, its heating area is almost square. If
the device to be heated is rectangular, the adjacent device will suffer from secondary tin melting.
It can be seen that the equipment using infrared heating technology cannot meet the basic requirements of lead-free soldering due to its
insurmountable shortcomings, such as slow heating and cooling, poor uniformity, and high thermal inertia of the heating body.
(2) Hot air heating equipment
Hot air reflow soldering is the key to the whole rework process, and there are several important issues. First, the curve of chip rework and
reflow soldering should be close to the original soldering curve of the chip. The hot air reflow soldering curve can be divided into four
sections: preheating zone, heating zone, reflow zone, cooling zone, the temperature of the four zones, Time parameters can be set separately.
Second, during the reflow soldering process, the heating temperature and time of each zone should be correctly selected, and the speed of
heating should be paid attention to at the same time. Generally, before 100°C, the maximum heating rate does not exceed 6°C/s, after 100°C,
the maximum heating rate does not exceed 3°C/s, and in the cooling zone, the maximum rate does not exceed 6°C/s. Excessive heating and
cooling speeds may damage PCBs and chips, and this damage is sometimes invisible to the naked eye. Different chips and solder pastes should
choose different heating temperature and time. For example, the reflow temperature of CBGA chip should be higher than that of PBGA. For
no-clean solder paste, its activity is lower than that of non-no-clean solder paste, so the soldering temperature should not be too high, and the
soldering time should not be too long to prevent the oxidation of solder paste particles. Third, in hot air reflow soldering, the bottom of the PCB
board must be able to be heated. The purpose of this heating is twofold: to avoid warping and deformation due to the heating of one side of
the PCB board; to shorten the melting time of the solder paste. For large-size board rework BGA, this bottom heating is especially important,
one uses hot air heating and infrared heating. The advantage of hot air heating is uniform heating, which is recommended for general rework
process. The disadvantage of infrared heating is that the PCB is not heated evenly. Fourth, choose a good hot air reflow nozzle. The hot air
reflow nozzle belongs to non-contact heating. When heating, the solder paste of each solder joint on the BGA chip is melted at the same
time by relying on high-temperature air flow. This nozzle seals the BGA component, ensuring a stable temperature environment throughout
the reflow process, while protecting adjacent components from being damaged by convective hot air heating (as shown). Due to the complex
nozzle structure and high price of hot air reflow soldering, it is difficult for users to match them when purchasing.
(3) Whole-process controlled hot air heating compared with infrared heating
The table shows the comparison between the whole process controlled hot air heating and infrared heating. It can be seen that the whole
process controlled hot air heating is more reliable than infrared technology. It is not recommended to use hot plate and infrared preheating
device, because the thermal induction time, energy conversion rate and efficiency are completely inconsistent, and there is no ability to heat
up and keep warm to support the establishment and operation of complex temperature curves. However, it can heat the surface of the object
and can be used in limited use for large pieces of metal and grounded printed boards.
Comparison of Surface Infrared and Whole Process Control Hot Air Heating Technology
infrared heating
Whole process control hot air heating
High thermal inertia, so heat control is difficult
easy heat control
thermal inertia, the cooling process is almost uncontrollable
Easy cooling control
Depending on the chip material, the heat absorption varies greatly
Not affected by chip material
Heated by a point heat source, the circuit board is easily deformed
The circuit board is evenly heated and not easily deformed
2. BGA pad repair
Due to repeated rework or other reasons, the BGA pads are lifted or peeled off and must be repaired. The repair steps are as follows:
(1) Clean the area to be repaired, remove the invalid pad and a small connection, scrape off the residual glue, stains and burnt materials with
a knife, scrape off the solder mask or coating on the connection, and clean the area.
(2) Dip a small amount of flux at the required connection, clean it after tinning, and ensure that the overlapping length of the connection is not
less than twice the line width.
(3) Insert the connection of the new BGA pad into the original via hole, remove the solder mask, and properly handle it to keep it smooth. If
there is any fiber layer exposure or surface scratches, it should be processed first. The most important thing in this process is to ensure the
height. If necessary, the surface of the board should be micro-grinded to ensure that the height will not interfere with the replaced components.
Take care to remove the solder mask between the BGA pad and the wire or via to ensure a low profile.
(4) Select a BGA replacement pad. These new pads are made of copper foil, tinned on the top side, and adhesive on the bottom side. When
trimming, use a knife to carefully scrape off the adhesive, cut off excessive connections, place high-temperature tape on the top surface, place
the new pad on the designated position of the PCB, and use the tape to help locate it. Then use a bonding press with a suitable bonding tip to
apply pressure for repair.
(5) After completion, dip a small amount of flux to the overlapping part of the welding connection, solder the connection of the new pad to the
surface circuit of the PCB, apply mixed branches to overlap the welding connection, and then cure.
(6) Apply surface coating as required and conduct inspection.
3.BGA hot air rework process and soldering defects
(1) Rework tools use forceless movement techniques to remove components from the board. When rework begins, the vacuum pick-up tube is
lowered to sense component height and then raised to a specified height. The hot air nozzle heats the component to the solder paste reflow
temperature, the vacuum nozzle is lowered to a predetermined height, the vacuum is turned on, and the component is removed without
destroying the eutectic solder joint. After the components are removed, the temperature of the offset base plate of the rework tool should be
set to a temperature of about 150°C to heat the base plate evenly, reduce the temperature slope at the rework position, and prevent local
board warpage caused by a large temperature slope.
(2) Remove the solder paste on the pad until the surface of the pad is flat. Apply flux to the desired position, after preheating to the proper
position, use a solder paste vacuum tool to suck up the solder paste to the vacuum tube, then clean the pad with isopropyl alcohol to check for
damage. Use a lint-free brush to brush across the board to apply flux, place new components, and reflow. The temperature profile must comply
with the reflow profile recommended by the solder paste manufacturer. Due to the different heat absorption of different boards, the inner layer
and adjacent components are different, each component for rework should be individually formulated to minimize the risk of overheating,
insufficient heating or pad lift-off.
(3) Component placement and reflow are the most difficult. After applying flux to the socket, mounting components and reflowing the socket,
usually the components will be skewed. In various cases, component solder balls wetted unevenly within the pads on the board. It was believed
that the components were too light and moved around in the hot air nozzles. This phenomenon occurs even at the low airflows allowed by the
rework tool. To prevent component movement, the rework tool is programmed to leave the vacuum pick-up tube on top of the component after
placement until through the warm-up portion of the profile. When the reflow cycle begins, the vacuum tube retracts slightly, allowing the
component to wet the pad without damaging the solder joint. This method works well, but has some drawbacks. The height and weight of the
suction tube on the component can sometimes cause solder bridges during reflow. Vacuum pick-up tubes also seem to reduce the BGA's ability
to self-center.
During the rework of printed circuit boards and chips, the warping caused by the large temperature difference between the top and bottom of
the PCB is the main cause of soldering problems, such as virtual soldering and bridging. As shown in the figure, special support blocks are
required to prevent warping. Through Preheat to reduce temperature differences that can cause warping. The sheet will bow downward under
the pressure of the height reading and subsequently warp upward during heating. This meant having to add extra height with each step. Even
slight deformation of the board can cause problems, as can chip warping. The gap between PBGA and PCB board is generally 0.020 inches,
and even a deformation of 0.005 inches in the chip range is enough to cause virtual soldering; the larger the device, the easier it is for these
problems to occur, and the closer to the middle of the chip, the more serious the problem. Bridging usually occurs at the peripheral solder
joints of the chip, especially at the four corners. Even if the board and chip are soldered without apparent problems, the return of the board to
its normal position will create constant tension on the solder joints, leading to long-term reliability problems.