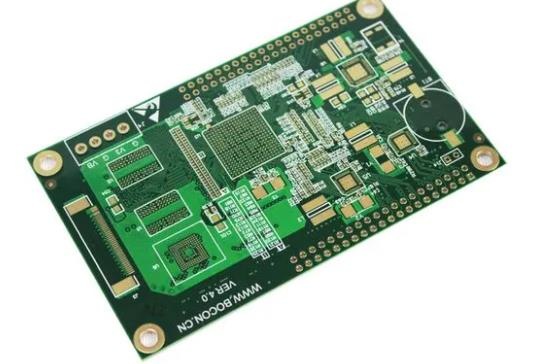
What is a good PCB design process? Now let me tell you
The process of PCB design and manufacturing is a complex and extensive process, and sometimes it is easy to forget the various tasks completed finally. We will take you to understand the core stages and related tasks undertaken by PCB designers, and discuss some challenges they encounter.
Phase I – Feasibility and Assessment
First of all, we must consider the relationship between the mechanical enclosure and the SCH circuit area, and determine how much circuit board space is required to optimally place and route the circuit. At this stage, it is also important to establish the density and determine how many routing layers may be required. Here, we can sometimes weigh our options; Depending on the circuit density, wiring can be done on fewer layers, but it will take longer. Then, we need to consider whether this is suitable for product launch or whether it can be reconsidered in the future to reduce costs/develop products.
The next step is to establish the design rules and restrictions of PCB manufacturers. After we have made our own assessment of the needs of the products we think, we can really communicate with the PCB manufacturing team to obtain their suggestions.
Then, the designer will establish the PCB assembler's design rules and restrictions, and determine the key circuit and power supply mapping. These will determine the component distribution at placement.
Stage 2 – Component placement/floor planning
So far, we begin to place key components. That is, the interconnection of the core processor with other boards/products and any other auxiliary mechanical functional interfaces, which we then review. Periodic reviews are continuous throughout the design phase, and interaction with the mechanical team is critical. Then, we worked with the engineer in charge to determine the exact wiring requirements, current, high-speed and impedance matching.
Stage 3 – Prioritize layout/divide design
At this point, we need to determine which circuits need to be wired first, such as those requiring a lengthy approval process. From these, we can make a sample board of the circuit and identify it, while the rest of the design is still going on. Depending on your software capabilities, it may be possible to divide the design into multiple parts and allow multiple designers to work in different areas in parallel, saving time. The best time to do this is after placement and before routing.
Phase 4 – Routing
The wiring of the circuit board needs to be evaluated with all responsible engineers to ensure that any circuit simulation/circuit change findings are included in a timely manner. This includes providing copper shapes for high current circuits and ground planes to form return current paths. The frequency of through hole stitching or reinforcement between repeated copper shapes depends on the circuit requirements and the balance of material stacking. Some consideration also needs to be given to the heat balance, because too many copper connections on multiple layers of the same hole will hinder the welding process
Stage 5 – Design Rule Review
We are now in the stage of completing the routing completion check, which usually runs in the entire routing stage. DRC element to element inspection and 3D mechanical alignment inspection were also performed to ensure that the layout not only meets the design rules, but also meets the requirements mechanically.
Phase 6 – PCB Design Simulation and Partner Review
After the priority of wiring sequence has been determined according to our product and project plan in the previous stage, the typical stages of PCB design may include:
High speed and impedance matching routing that may require a clean path from A to B may be preferred.
Power distribution: If there are any defects in the component placement phase (phase 2), you need to know as soon as possible, so please start power distribution until the end. Have you created a bottleneck?
Small signal routing, analog and digital.
Other wiring tasks will include adding large copper shapes for high current guides, grounding loops, and through seams.
Test point assignment.
All the above contents can be mixed together, and are usually concurrent/parallel tasks. Experienced designers will have a good sense of priority based on the layout stage, but one technique that is often overlooked is simply asking the design team if they know of any pending changes. There may be significant design changes in the pipeline that the design team is working on, which means that the time spent on routing this specific area will be wasted.
Phase 7 – PCB design output/completion
At this stage, the final inspection and evaluation will be carried out. Repeat DRC checks, process all required outputs, distribute information to all relevant recipients, and lock the design as "released".
Phase 8 – Incoming project queries
It is hoped that by pre publishing the data to PCB manufacturers, any engineering queries that may delay production can be eliminated. However, if there are queries that really need design intervention, the severity needs to be evaluated with management. It may be necessary to return to the Simulation and Review phase.
Phase 9 – PCB design prototype
This is the time when the first prototype is built and tested. Any information from PCB manufacturing or product assembly that may cause process problems shall be fed back to the designer as soon as possible. According to your product development strategy, the next iteration of PCB is usually started immediately after the release of the first prototype. Because many problems do not appear until the later stage of the test phase, PCB designers may be under great pressure. Combine the latest changes and deliver on time. This is the time to apply good change, review, and release methods. The PCB processing factory explains the process of PCB design and manufacturing, and what is a good PCB design process.