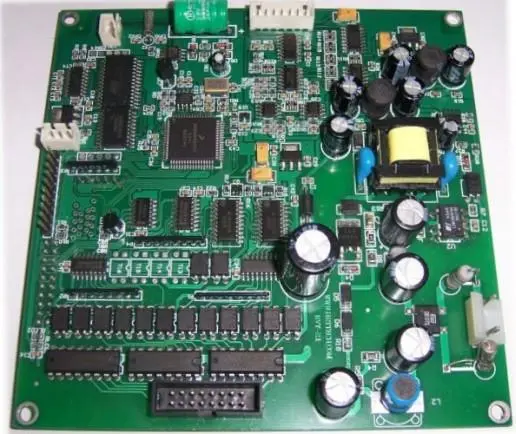
Now half of the production circuit boards will require testing, and there are two common methods for complex PCB design at present, the needle bed test method and the double probe or flying probe test method. The following is a summary of the relevant features, which should be understood if necessary.
With the introduction of surface mount technology, the packaging density of circuit boards increases rapidly. Therefore, even for low density and average number of circuit boards, the automatic detection of circuit boards is not only basic, but also economical. In complex PCB testing, two common methods are needle bed testing and double probe or flying probe testing.
Needle bed test method
This method is connected to each detection point on the circuit board by a probe with a spring. The spring makes each probe have a pressure of 100 - 200g to ensure good contact of each detection point. Such probes are arranged together and called "needle bed". Under the control of the detection software, the detection points and detection signals can be programmed. Figure 14-3 is a typical structure of the needle bed tester. The detector can obtain the information of all test points. In fact, only the probes at the test points that need to be tested are installed. Although the needle bed test method may be used to test both sides of the circuit board at the same time, when designing the circuit board, all the test points should be on the welding surface of the circuit board. Needle bed tester is expensive and difficult to maintain. The probes with different arrangements are selected according to their specific applications.
A basic universal grid processor is composed of a PCB drilling board, and the center spacing of the pins on the board is 100, 75, or 50 mil. The pin acts as a probe and uses the electrical connector or node on the circuit board for direct mechanical connection. If the pad on the circuit board matches the test grid, then the polyacrylate film perforated according to the specification will be placed between the grid and the circuit board to facilitate the design of specific detection. Continuity detection is achieved by accessing the end point of the mesh (defined as the x-y coordinate of the pad). Since each network on the circuit board is tested for continuity. In this way, an independent detection is completed. However, the proximity of the probe limits the effectiveness of the needle bed test method.
2 Double probe or flying probe test method
The flying probe tester does not depend on the pin pattern installed on the fixture or bracket. Based on this system, two or more probes are mounted on a small magnetic head that can move freely on the x-y plane, and the test points are determined by CADI
Gerber data is directly controlled. The double probes can move within a distance of 4mil from each other. The probes can move independently without really limiting how close they are to each other. The tester with two movable arms is based on capacitance measurement. Press the circuit board tightly and place it on the insulating layer of a metal plate as another metal plate of the capacitor. If there is a short circuit between lines, the capacitance will be greater than at a certain point. If there is an open circuit, the capacitance will decrease.
Test speed is an important standard for selecting a tester. The needle bed tester can accurately test thousands of test points at a time, while the flying needle tester can only test two or four test points at a time. In addition, the needle bed tester may only spend 20 - 305 for single side testing, which depends on the complexity of the board, while the flying needle tester requires IH or more time to complete the same evaluation. Shipley (1991) explained that even though manufacturers of high-yield printed circuit boards think that the mobile flying probe testing technology is slow, this method is still a good choice for manufacturers of low yield complex circuit boards.
For bare board testing, there are special testing instruments (Lea, 1990). A more cost optimized method is to use a general instrument. Although this kind of instrument is more expensive than the special instrument at first, its initial high cost will be offset by the reduction of individual configuration costs. For the general grid, the standard grid for boards with pin components and surface mount devices is 2.5mm. At this time, the test pad should be greater than or equal to 1.3mm. For the grid of Imm, the test pad shall be designed to be greater than 0.7mm. If the grid is small, the test pin is small, brittle and easy to damage. Therefore, grids larger than 2.5mm are preferred. Crum (1994b) clarified that the combination of a universal tester (standard grid tester) and a flying probe tester can make the detection of high-density circuit boards accurate and economical. Another method he suggested was to use a conductive rubber tester, a PCB technology that can be used to detect points that deviate from the grid. However, the height of pads leveled by hot air is different, which will hinder the connection of test points.
Generally, the following three levels of detection are carried out:
1) Bare plate detection;
2) Online detection;
3) Function test.
The universal tester can be used to test a class of style and type of circuit boards, and can also be used for testing special applications.