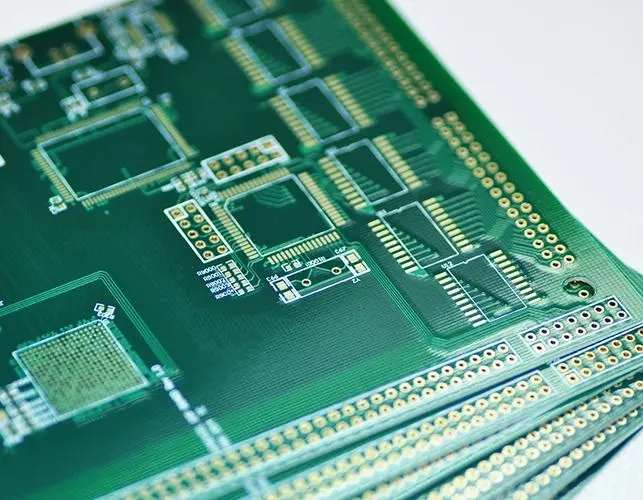
Detailed explanation of PCB design rules for analog circuits
Although building analog systems looks like a return to the era of vacuum tubes, analog components and circuits will not disappear soon, nor will the PCBs that support them. Pure analog circuit boards and mixed signal PCBs are still important in many products and will continue to operate at a range of frequencies. Getting started with simulating PCB design and what to consider may be difficult, but we hope these guidelines will help you understand what steps you can take to ensure success.
Sometimes it is best to consider analog PCB and mixed signal PCB based on common design goals. Analog circuits and PCBs require special care because the goal is usually to route signals and input them into components/circuits while ensuring low noise operation. Then, the frequency range of the circuit board operation will determine some measures that need to be taken to ensure that the design operates as expected. In this guide, we will outline some standard analog PCB design and layout guidelines that you should consider. We will try to cover from low kHz frequency to high millimeter wave frequency.
Analog PCB layer stacking
After the circuit is designed, the layer stack is the first stop of the design. Analog layer stacks usually follow the same idea used to build digital PCB stacks. Pay attention to the following points:
Power and grounding: It is planned to use a large number of grounding around the routing of critical signals in the PCB layout, and plan the power rail wiring accordingly. Newer designers may be used to thinking about how to route important analog interconnects, but if you do this early, you can plan power and signal cabling accordingly.
High frequency power supply: If your analog board needs to transmit with high output power and high frequency, you need to provide a very stable power supply, which may be high current. It is planned to use the power layer instead of the guide rail on the internal layer and place the ground plane on the adjacent layer.
Material selection: I think every designer wants to use low loss PTFE based laminate for each layer of analog circuit board, but these expensive materials are not always necessary. If your operating frequency is not dozens of GHz, and you only use shorter cabling, you can use standard FR4 laminates as long as you do not cable long interconnects. If you do need low loss laminates, contact your manufacturer to learn how to use mixed PCB stacks.
Today's analog boards usually contain a digital part on the same board as the analog part. How should you handle this in your stack? In a mixed signal PCB, the recommendations for power and ground are usually different, depending on whether your analog and digital parts need any direct wiring between them.
Mixed signal grounding
If your circuit board also has a digital part, things will become more complicated in your component placement. In general, because of the speed of digital circuits, you should not use a physically separated ground plane, but a single ground plane. Try to plan your layout so that the return paths of digital and analog blocks are naturally separated. This is difficult at low frequencies, which is why so many design guidelines continue to advocate the use of separate analog and digital ground planes.
Mixed signal power supply
For mixed signal power supply, the power plane is usually divided into digital and analog parts, similar to the work done by the digital power plane working under different supply voltages. These parts shall be located in the same layer and refer to the same ground plane on adjacent layers. In addition, it is better to place the digital power rail only on the digital part of the circuit board, as is the case with the analog power rail.
In addition, you should not create an interface between digital and analog parts by wiring the gap between them. To find out why, check out this article. The interface you need can be provided by ADC, which may be built-in in your host controller or it can be a special IC.
Simulate component placement in PCB layout
Unfortunately, we cannot cover the placement of all possible components, but we can briefly discuss some important components. The two most interesting components with some important layout guidelines are the ADC and amplifiers (including operational amplifiers). Although I would like to mention PLL here, these circuits depend on a large number of clock routing and precise timing, so it is better to write a separate article.
Handling unused operational amplifiers
One component that must appear on the analog board is the operational amplifier. In many operational amplifier ICs, some operational amplifiers will be idle. Any unused leads on the IC should be properly terminated. Unterminated (i.e. floating) leads on the operational amplifier in the IC will generate noise and propagate to the working IC, thereby reducing signal integrity.
If you are using a single power rail, you should first short the output to the sinking input. This produces negative feedback and ensures that the output follows the input correctly. Next, connect a voltage divider with equal resistance to the in-phase input and ground pins. This sets the input potential to the midpoint of the linear range. If you use a split rail, you can simply short the output to the sinking input and ground the in-phase input.
Problems with power amplifiers
At low frequencies, the amplifier will not be subject to any special restrictions not applicable to other PCBs. For power amplifiers operating at high frequencies, the situation is different because the amplifier output may be unstable, which may be an unexpected positive feedback. You can use some simulations to track coupling back to amplifier inputs, although these require a field solver that can interface directly with your PCB layout. To learn more about this interesting signal integrity issue involving RF power amplifiers.
Location of ADC
ADC is the place where your analog signal connects with the digital world, so this part needs to be placed carefully, because it will contain the digital part. The split ADC is best placed roughly along the boundary between the digital and analog parts. In fact, this may be the only acceptable way to create an interface in a mixed signal system with separate ground planes, since the ground plane on the silicon chip can provide a reference plane for input/output signals. However, if you use a uniform ground plane, placement of the ADC and the shielding provided by the ground plane will have greater flexibility.
Analog PCB Wiring Guide
The wiring in the analog PCB is to ensure that the analog signal sent along the interconnection will not be significantly distorted on the receiver side of the interconnection. When using analog PCBs, your net count is usually much less than in digital PCBs, so you can try some possible layouts as early as possible until you find a solvable plan. Here are some route guides to help you:
Routing length: In general, try to keep the routing in the analog PCB short and straight. With the increase of signal frequency, this is very important. In addition to the loss, pay attention to the critical length of the signal.
Forced impedance matching: Even if your routing length is very short, forced impedance matching is still a good idea anyway. This may mean that you need to design some impedance matching networks on important circuits or components to ensure non reflective power transmission between circuits.
Consider coplanar wiring: You can use coplanar PCB wiring to ensure high isolation without sacrificing impedance. You can still force impedance control while violating the "3W" clearance rule for copper casting.
Minimize the use of vias: Each vias will increase the loss of interconnect S parameters, so it is best to minimize these losses and, if possible, only perform the necessary layer conversion. For those vias that still exist, they may generate strong radiation like antennas
Depending on the dominant frequency you will use in the circuit board, you may consider routing through the internal layers between planar layers. When isolation is required, higher frequency striplines or coplanar wiring on the inner layer is preferred, as long as via conversion is minimized. Make sure that your via size is appropriate, and the spacing between it and the plane with reverse pad is suitable for your working frequency, although this is easy to say, difficult to do, and not easy to calculate. This particular point should be checked by measurement (S parameter), because nearby planes and other conductors will modify the via impedance during signal conversion to the inner layer.
There are many issues to consider in analog PCB layout, but the correct design tools and rule driven design software will help you implement the required guidelines to keep the analog system noise free and ensure signal/power integrity. The circuit board assembly and circuit board processing manufacturers explain where to start and what to consider for the introduction of analog PCB design.