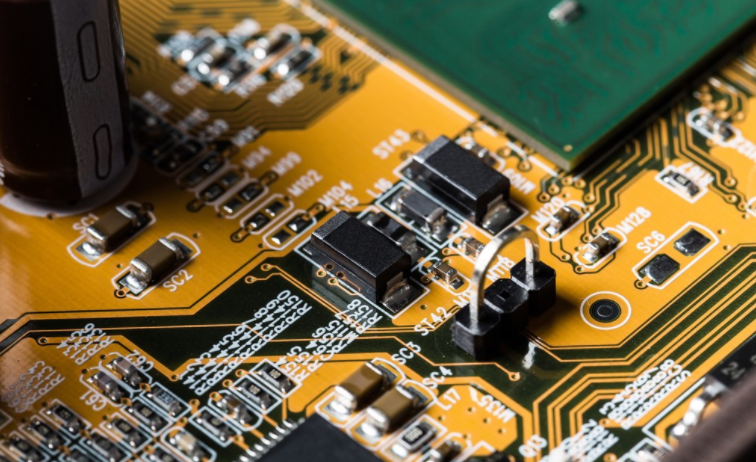
Improvement Measures for OSP Surface Treatment PCB
1 Choose the right OSP potion
OSP has three types of materials: Rosin, active resin and azole At present, the most widely used is oxazole OSP The oxazole OSP has been improved for about 6 generations, and its decomposition temperature can reach 354.9 ° C, which is suitable for lead-free process and multiple reflow soldering Before PCB production, it is necessary to select appropriate agents according to the production process of the product
2. During PCB production, the thickness and uniformity of OSP film must be strictly controlled
The key of OSP process is to control the thickness of protective film. The thickness of the film is too thin and the thermal shock resistance is poor. In the process of reflow soldering, the thin film cannot withstand high temperature, cracking and thinning, which easily leads to pad oxidation and affects solderability; If the film thickness is too thick, it will not be good during welding. The dissolution and removal of flux can also lead to poor welding.
3. OSP board production process
Placement of circuit board - degreasing - cleaning - micro etching - cleaning - pre soaking - deionizing cleaning - liquid suction - upper protective film (OSP) - liquid suction - deionizing cleaning - drying - drying - drying - unwinding
4. Main factors affecting OSP film thickness
-A. Degrease. The degreasing effect directly affects the film quality. Poor degreasing will lead to uneven film thickness. On the one hand, the concentration can be controlled within the process range by analyzing the solution. On the other hand, always check whether the degreasing effect is good. If the degreasing effect is not good, replace the degreasing liquid in time.
Circuit board
b. Microetch. The purpose of micro etching is to form a rough copper surface to promote the formation of thin films. The thickness of micro etching directly affects the film forming rate. In order to form a stable film thickness, the thickness of micro etching must be kept stable. In general, it is appropriate to control the micro etching thickness at 1.0~1.5 um. Before each shift, the micro corrosion rate must be measured and the micro corrosion time must be determined according to the micro corrosion rate.
c. Pre soak. Pre soaking can prevent harmful ions such as chloride ions from damaging the OSP tank solution. The main function of OSP prepreg cylinder is to accelerate the formation of OSP film thickness and deal with the influence of other harmful ions on OSP cylinder. The prepreg solution contains an appropriate amount of copper ions, which can promote the formation of composite protective film and shorten the dip coating time. It is generally believed that due to the presence of copper ions, alkylbenzimidazole and copper ions have been complexed to a certain extent in the pre flux solution. When the complex with a certain degree of aggregation is deposited on the copper surface to form a composite film, a thick protective layer can be formed in a short time, thus acting as a complexing accelerator. For example, the content of alkyl benzimidazole or similar components (imidazole) in the prepreg is very low. When the copper ion is excessive, the prepreg solution will age prematurely and need to be replaced. In this regard, it is necessary to focus on the control of prepreg concentration and prepreg time.
d. The concentration of the main components of OSP. Alkyl benzimidazole or similar components (imidazole) are the main components in OSP solution, and the concentration is the key to determine the thickness of OSP film. During the production process, it is necessary to focus on monitoring the concentration of OSP solution.
e. PH value of the solution. The stability of pH value has a great influence on the film forming rate. In order to maintain the stability of pH value, a certain amount of buffer is added to the solution tank. Generally, when the PH value is controlled between 2.9 and 3.1, dense, uniform and medium thickness OSP films can be obtained. When PH value is high and PH>5, the solubility of alkyl benzimidazole decreases and the oil precipitates; When PH value is low and PH<2, the formed membrane will be partially dissolved. It is necessary to focus on monitoring the PH value.
f. Temperature of the solution. The change of temperature also has a great influence on the film forming rate. The higher the temperature is, the faster the film is formed. In this case, it is necessary to control the temperature of the OSP tank.
g. Film forming time (dip coating time). Under certain OSP bath composition, temperature and pH value, the longer the film forming time is, the thicker the film is. It is necessary to control the film forming time.
5. OSP film thickness detection
At present, most PCB factories use ultraviolet ultraviolet spectrometer to measure the thickness of OSP film Its principle is mainly to use the strong absorption characteristics of imidazole compounds in OSP film in the ultraviolet region, and then measure the absorbance at the maximum time The method is simple and easy to calculate OSP film thickness, but the measurement error is relatively large Another method is to use FIB technology to measure the actual thickness of the OSP film [6]. PCB factories need to use appropriate methods to detect and control the thickness of OSP film in the production process to ensure that the thickness of OSP film meets the standard requirements
Packaging and storage requirements for OSP boards
Because the OSP film is very thin, if it is exposed to high temperature and humidity for a long time, the PCB surface will be oxidized and the solderability will deteriorate. After reflow soldering, the OSP on the PCB surface will also crack and become thin, which easily leads to PCB copper foil oxidation and degrades solderability.
6.1 Packaging requirements for OSP board
The incoming materials of OSP board shall be vacuum packed, and attached with desiccant and humidity display card. Separate the PCB from the circuit board to avoid scratching or friction damage to the OSP film.
6.2 Storage requirements of OSP board
It cannot be directly exposed to the sun. It shall be stored in an environment with a relative humidity of 30-70% and a temperature of 15-30 ℃. The warranty period is less than 6 months. It is recommended to use special moisture-proof cabinet for storage. If the PCB is wet or expired, it cannot be baked and can only be returned to the PCB factory for OSP rework.
7. Use of OSP board in SMT section and precautions
a. Before opening the PCB, check whether the PCB package is damaged and whether the humidity instruction card is discolored. Do not use if damaged or discolored. It needs to be put into production within 8 hours after opening. It is recommended to use as many openings as possible. For the PCB that has not been produced or the last number of PCBs, vacuum packaging should be used in time.
b. It is necessary to control the temperature and humidity of SMT workshop. Recommended workshop temperature: 25 ± 3 ℃, humidity: 50 ± 10%. During the production process, it is prohibited to directly touch the PCB pad surface with bare hands to prevent sweat pollution, which may lead to oxidation and poor welding.
c. The printed circuit board of the solder paste should be installed as soon as possible and pass through the furnace to avoid cleaning caused by printing errors or installation problems, because cleaning will damage the OSP film. When cleaning, it is recommended to wipe the solder paste with non-woven cloth dipped in 75% alcohol. The cleaned PCB must be welded within 2 hours.
d. After placement of SMT on one side, placement of SMT components on the second side shall be completed within 24 hours, and selective welding or wave soldering of DIP (plug-in) components must be completed within 36 hours.
e. Because PCB treated with solder paste OSP has poor fluidity compared with PCB treated with other surfaces, copper may be exposed at solder joints When designing the mold opening, it can be added appropriately It is recommended to open a hole of. 05 or 1:1.1 according to the 1:1 ratio of the gasket, but you need to pay attention to the tin bead prevention treatment of the chip assembly
f. When the welding quality is satisfied, it is recommended that the peak temperature and reflow time of the OSP board during reflow welding should be as close to the lower limit of the process window as possible, and the peak temperature and reflow time should be as low as possible; When producing double-sided boards, it is recommended to reduce the first side (the temperature on the component side is lower) and set the temperature on both sides respectively to reduce the damage to the OSP film caused by high temperature. If possible, it is recommended to use nitrogen for production, which can effectively improve the oxidation and poor welding of the second side of the double-sided OSP plate.