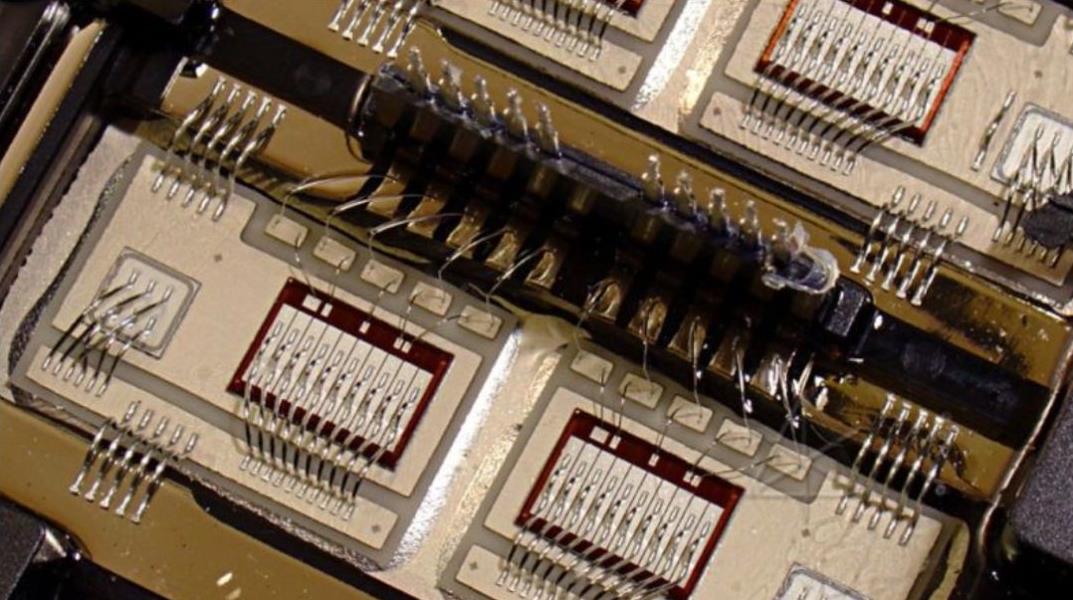
PCB screen printing board manufacturing technology
Manufacturing technology of screen printed circuit board
Printed circuit board bandage
Binding steps of printed circuit board: frame cleaning -- leveling verification -- layered gel -- pull wire -- tension measurement -- glue -- offline, edge sealing -- storage
Job description:
1. Due to the repeated use of the grid, there are adhesive, mesh and other impurities left around the grid, which must be cleaned to avoid affecting the adhesion between the mesh and the grid.
2. Place the grid on the platform (level) and check whether the grid is deformed. If it is deformed, it needs leveling.
3. Clean the untouched grid and mesh, and then apply a layer of glue without hardener to enhance the adhesion between the grid and mesh after the mesh is pulled.
4. About 10 minutes after the first gluing, place the grid on the traction platform and adjust the relative position and height
5. Select the mesh, loosen the surrounding clips, place the mesh flat on the frame, and then clip the mesh evenly into the clips without wrinkles. Note that the mesh around the corner is loose, the clips must be locked, and there must be no gap between the clips (for example, automatic lifting frame, manual mesh pulling).
6. Tension: 26 for the first time, 24 for 5 minutes; The tension was 28 for the second time and 26 after 5 minutes of rest. The tension was 32 for the third time and 30 after 5 minutes of rest. For the fourth time, correct the five point tension 32, and apply glue tension 30 after a 20 minute rest. After the gel is cured for 15 minutes, the mesh tension is 28, and it can only be made (within one meter) after 72 hours of rest. For example, * 1 meter full-automatic production line uses the screen. The tension of common screen yarn is (30+2N for 100 T, 110 T and 120 T) (35+2N for 77 T and 51 T) (50+2N for 24 T)
7. Use a small brush to evenly brush the prepared glue on the net and the side of the net. Do not drop glue in the middle of the net. After drying for 8 minutes, you can use the scraper glue to press the glue into the position that is not completely suitable for about 10 minutes, and then the glue is completely dried (outdoor drying should be used to enhance the drying).
8. Use the paper cutter to remove the extra grid around the screen, and mark the date, grid and tension when leaving the screen (to observe the change of tension). To prevent the penetration of grid cleaning water (white water), seal the inner corner of the frame with red glue, and then seal the next surface of the frame and screen with waterproof tape, which can also prevent drug penetration.
PCB mask
Printed circuit board sunscreen
1. Clean the mesh: remove the grease (new mesh) with grinding paste, remove the graphics (old mesh) with gypsum, remove the mesh slurry and blue oil with pulp powder, clean the impurities with anti white water, wash the mesh with detergent, wash with high-pressure water gun, and finally clean with pure water.
2. Drying: The setting temperature of the oven should be lower than 48 ℃.
3. Use the film sticking method: clean the screen and clean it again with clean water. According to the mosaic pattern of the engineering membrane, 20% of the newly added water membrane is selected. Press one end of the water film onto the net with a 3 angle ruler, then slowly scrape it with a 3 angle ruler, gently scrape it with a rubber scraper, and then wipe off the excess water with a towel.
4. Use of photosensitive adhesive (screen paste): after drying the screen board, apply photosensitive adhesive, and scrape the screen with the scraping ink box. The screen printing green oil needs to be pasted 3 times (about once every 10 minutes or more), and the screen printing uses other anti-corrosion ink twice. Screen printing peel off glue (orchid glue): tear off the film with 50 micron water film, then tear the screen paste twice, scrape it three times each time, and dry it after pasting.
5. The selection of universal wire for screen yarn includes character ink screen printing, 120T, 100T, 110T anti-corrosion ink (green oil, base oil, top oil) screen yarn, 51T carbon syrup (carbon oil), 24T screen printing separation ink (blue glue) photosensitive wire and 77T heat curing ink.
6. 18K water-based film for film wire selection (photosensitive adhesive without photosensitive adhesive is easy to surf the web unevenly: such as rough edges (canine teeth), etc.). Other anti-corrosion inks (green oil, base oil, flour oil) use photosensitive adhesive (mesh paste), and carbon paste (carbon oil) uses 50 micron water-based membrane.
7. Paste the required engineering graphics film on the web at the selected position, and place it on the sandblasting machine for sandblasting. Select the time (3000W spotlight). The lines are generally 60-80 seconds, the green oil is 80-100 seconds, the base character oil is 40-60 seconds, the carbon oil is 350-400 seconds
8. Rinse and dry with pressurized water.
9. When making the screen, use sealant (blue oil) to dry the area where the screen is not covered by the film or photosensitive adhesive.
10. Check, repair, record the completion date and corresponding number, and make records, filing and keeping.
PCB mask
PCB screen board storage
Storage is usually vertical. You can make or buy the grid yourself. It needs to be stored in the same environment as the screen printing environment to prevent deformation. At the same time, you need to test the screen tension before printing, and you can use photographic film to check the graphics.
The above is the explanation given by the editor of pcb circuit board company.
If you want to know more about PCBA, you can go to our company's home page to learn about it.
In addition, our company also sells various circuit boards,
High frequency circuit board and SMT chip are waiting for your presence again.