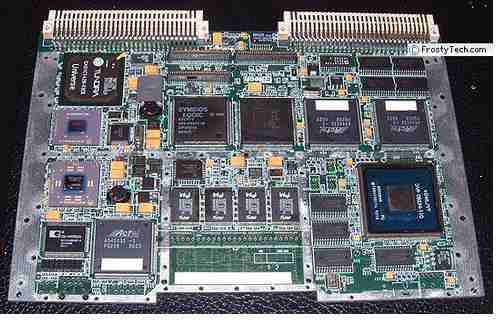
What are the requirements of the solder paste printing process for the SMT patch factory
In the field of electronic manufacturing, SMT chip processing is a very important process. The solder paste printing process is also a key link that affects the quality of electronic products. Therefore, the SMT processing plant has strict requirements and standards for the solder paste printing process. This article will introduce in detail the requirements of the solder paste printing process of the SMT patch factory, in order to improve the quality and reliability of electronic products.
1. Selection of solder paste
Before the solder paste printing process, the SMT paste processing factory must first select the solder paste suitable for its own production. First of all, the viscosity of the solder paste should be moderate, neither too thick nor too thin. Too thick solder paste will affect the accuracy and efficiency of printing, too thin solder paste will flow phenomenon, affecting the welding effect. Secondly, the solder paste should have good adhesion and weldability, which can ensure that the components can be firmly adhered to the PCB, and the solder joint can be firm and reliable. In addition, the composition and quality of the solder paste should also meet the relevant standards and requirements to ensure that the products produced meet national and industry standards.
2. Production of printing templates
The SMT patch factory also makes printing templates to ensure the accuracy and stability of printing. The production of printing templates requires the use of high-precision processing equipment, and the use of high-precision optical inspection instruments to detect the accuracy and smoothness of the templates. The thickness and aperture of the printing template also need to be precisely controlled according to the specific product requirements. Only by producing high-quality printing templates can we ensure the effect and stability of printing.
3. Control of printing process
In the solder paste printing process, the SMT patch processing plant also needs to control a series of printing process parameters to ensure that the quality of the final product meets the requirements. For example, printing speed, printing pressure, printing height, printing Angle and other parameters need to be precisely controlled. In addition, when printing, it is also necessary to use high-precision printing presses and precise printing technologies, such as holographic projection technology and linear motor technology. Only through strict process control can high quality electronic products be produced.https://www.kingfordpcb.com/yuan.php
4. Quality inspection and control
After the solder paste printing process, the SMT patch processing plant also needs to strictly inspect and control the printing quality. Common detection methods include visual detection, microscope detection, optical detection, X-ray detection and so on. Only by carrying out accurate quality inspection can we screen out the unqualified products of printing quality and correct the problems in time. In addition, SMT processing plants also need to use relevant quality management systems and testing equipment in the quality control process to track and monitor the printing process.
In short, SMT processing plants have very strict requirements and standards for the solder paste printing process. Only by comprehensive and strict production control and quality management can we produce high quality and high reliability electronic products. Therefore, if you want to choose a professional SMT processing plant to produce your electronic products, you must choose a manufacturer with a good reputation and rich experience to ensure the quality and performance of the product.