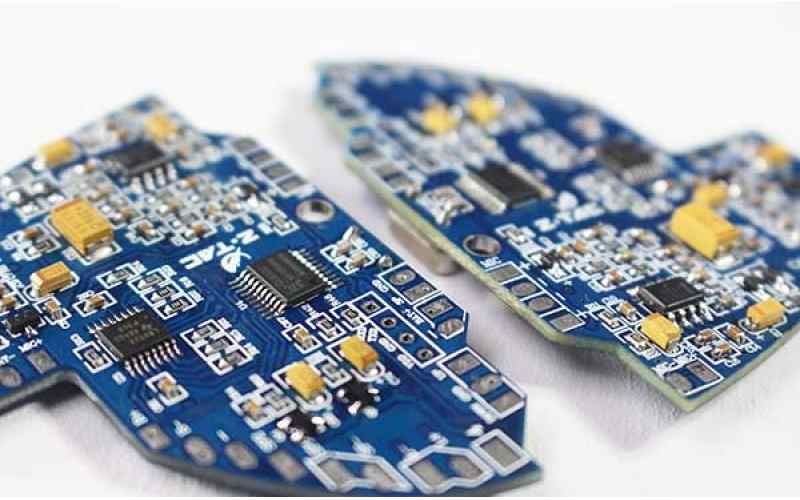
With the continuous increase of chip input power, high heat dissipation power brings new and higher requirements for packaging materials. In the heat dissipation channel, the packaging substrate is the key link to connect the internal and external heat dissipation channels, and has the functions of heat dissipation channel, circuit connection and physical support for the chip. For high-power products, the packaging substrate is required to have high electrical insulation, high thermal conductivity, and thermal expansion coefficient matching with the chip.
In recent years, the rise of the patch type bracket generally uses high temperature modified engineering plastic material, with PPA (polyphthalamide) resin as raw material, by adding modified filler to enhance some of the physical and chemical properties of PPA raw material, so that PPA material is more suitable for injection molding and the use of the patch type bracket. PPA plastic has very low thermal conductivity, and its heat dissipation is mainly carried out through the metal lead frame, which has limited heat dissipation capacity and is only suitable for low-power packaging.
As the industry pays more attention to heat dissipation, two new thermosetting plastics, Epoxy Plastic (EMC) and Sheet molding plastic (SMC), have been introduced into the SMT bracket. EMC is a powder molding plastic made of high performance phenolic resin as curing agent, silicon powder with high thermal conductivity as filler and a variety of additives. SMC is mainly composed of about 30% unsaturated resin, about 40% glass fiber, inorganic filler and other additives.
These two kinds of thermosetting plastic hot curing temperature at about 150℃, after modification of thermal conductivity can reach 4W/ (m·K) ~ 7W/ (m·K), compared with PPA plastic has a large increase, but the disadvantage is that the fluidity and thermal conductivity is difficult to take into account, curing molding hardness is too high, easy to produce cracks and burrs. EMC and SMC have long curing time, relatively low molding efficiency, and high requirements for molding equipment, molds and other supporting equipment. The price of a molding and supporting production line is about 10 million yuan, so it is still difficult to popularize on a large scale.
Silicon - based packaging substrate: facing the challenge of good product rate below 60%. The silicon substrate faces challenges in the preparation of insulating layer, metal layer and through-hole, and the yield is not more than 60%. Silicon - based materials as packaging substrate technology, in recent years from the semiconductor industry gradually introduced to the industry. The thermal conductivity and thermal expansion of silicon substrate indicate that silicon is a suitable packaging material.
The thermal conductivity of silicon is 140W/m·K, and the thermal resistance caused by packaging is only 0.66K/W; Moreover, silicon-based materials have been widely used in semiconductor process and related packaging fields, and related equipment and materials have been quite mature. Therefore, if silicon is made into packaging substrate, it is easy to form mass production. However, silicon substrate packaging still has many technical problems. For example, in terms of materials, silicon is prone to cracking and has problems with institutional strength. In terms of structure, although silicon is an excellent heat conductor, it has poor insulation and must be treated with oxidation insulation.
With the development of packaging to thin and low cost, chip on board (COB) packaging technology is rising gradually. At present, COB packaging substrate mostly uses metal core printed circuit board, high power packaging mostly uses this substrate, its price is between the middle and high price. The thermal conductivity of the insulation layer is very low. Moreover, the existence of the insulation layer makes it unable to withstand high temperature welding, which limits the optimization of the packaging structure and is not conducive to heat dissipation.
Metal core printed circuit board manufacturing process is complex and practical application is few. Aluminum substrate manufacturing process is complex, high cost, the thermal expansion coefficient of aluminum and chip material is much different, the practical application is rarely used. How to improve the thermal conductivity of epoxy insulation layer has become a research hotspot of aluminum substrate at present. Currently, a modified epoxy resin or epoxy glass cloth binder mixed with a heat-conductive inorganic filler, such as ceramic powder, is used to bind the copper foil, insulator and aluminum sheet together by hot pressing. At present, a kind of "all-rubber aluminum substrate" has been developed in the world. The thermal resistance of all-rubber aluminum substrate can be 0.05K/W. In addition, a company in Taiwan has recently developed a dril-like carbon material DLC and applied it to the insulation layer of high-brightness LED packaging aluminum substrate.
DLC has many superior material properties: high thermal conductivity, thermal uniformity and high material strength. Therefore, the replacement of epoxy resin insulation layer with DLC is expected to greatly improve the thermal conductivity of MCPCBS, but its practical application effect is still to be tested in the market.
A better performing aluminium substrate is to create an insulating layer directly on the aluminium substrate and then print the circuit. The biggest advantages of this method are strong binding force and high thermal conductivity of 2.1W/ (m·K). However, the manufacturing process of this aluminum substrate is complicated and cost is high. Moreover, the thermal expansion coefficient of aluminum metal is quite different from that of the chip material, and the thermal cycle of the device often produces great stress, which may eventually lead to failure, so it is rarely used in practical applications.
In addition, the metal layer shall be prepared by sputtering and electroplating, and the conductive hole shall be made by etching. Generally speaking, the preparation of insulating layer, metal layer and through-hole is faced with challenges, and the yield is not high. At present, although some Taiwan enterprises have developed LED silicon substrate and mass production, but the yield is not more than 60%.
Ceramic encapsulated substrate: improves heat dissipation efficiency to meet high power requirements
Combined with high thermal conductivity ceramic matrix, DPC significantly improves heat dissipation efficiency and is the most suitable product for high power and small size development requirements.
Ceramic heat dissipating substrate has new thermal conductivity materials and new internal structure, make up for the defects of aluminum metal substrate, so as to improve the overall heat dissipation effect of the substrate.
Al2O3 ceramic substrate is currently the most productive and most widely used ceramic substrate, but because its thermal expansion coefficient is higher than that of Si single crystal, Al2O3 ceramic substrate is not suitable for use in high frequency, high power and very large scale integrated circuit. A1N crystals have high thermal conductivity and are considered as ideal materials for the next generation of semiconductor substrates and packages.
AlN ceramic materials have been widely studied since the 1990s and developed gradually. It is widely considered as a promising electronic ceramic packaging material at present. The heat dissipation efficiency of AlN ceramic substrate is 7 times as much as that of Al2O3 substrate. The heat dissipation efficiency of AlN substrate applied to high power LED is significant, thus greatly improving the service life of LED.
The disadvantage of AlN substrate is that even if there is a very thin oxide layer on the surface, the thermal conductivity will be greatly affected. Only by strict control of the material and process can AlN substrate be manufactured with good consistency.
At present, ceramic substrates used in packaging can be divided into HTCC, LTCC, DBC and DPC4 according to the preparation technology. HTCC is also known as high temperature co-fired multilayer ceramics. Its main materials are tungsten, molybdenum, manganese and other metals with high melting point but poor electrical conductivity, which are expensive to make and rarely used now.
LTCC, also known as low-temperature co-fired multilayer ceramic substrate, has a thermal conductivity of about 2W/ (m·K) ~ 3W/ (m·K), which is not much advantage compared with the existing aluminum substrate. In addition, LTCC uses thick film printing technology to finish the line production, the surface of the line is rough and the alignment is not accurate. Moreover, the shrinkage ratio of laminated ceramic sintering process is also a problem, which limits the resolution of the process and challenges the popularization and application of LTCC ceramic substrate.
Direct copper clad ceramic plates (DBC) developed based on on-board packaging technology is also a ceramic substrate with excellent thermal conductivity. DBC substrate is prepared without the use of binder, so it has good thermal conductivity, high strength, strong insulation, and a thermal expansion coefficient matching Si and other semiconductor materials. However, the reaction ability of ceramic substrate and metal materials is low, poor wettability, implementation of metallization is quite difficult, it is not easy to solve the problem of micro-porosity between Al2O3 and copper plate, which makes the mass production and yield of the product by greater challenges, is still the focus of research workers at home and abroad.
DPC ceramic packaging substrate is also known as direct copper-plated ceramic plate. DPC products have the characteristics of high line accuracy and high surface smoothness, which is very suitable for LED coating/eutectic process. Combined with high thermal conductivity ceramic matrix, it significantly improves the heat dissipating efficiency, and is the most suitable ceramic heat dissipating substrate for high power and small size LED development requirements.