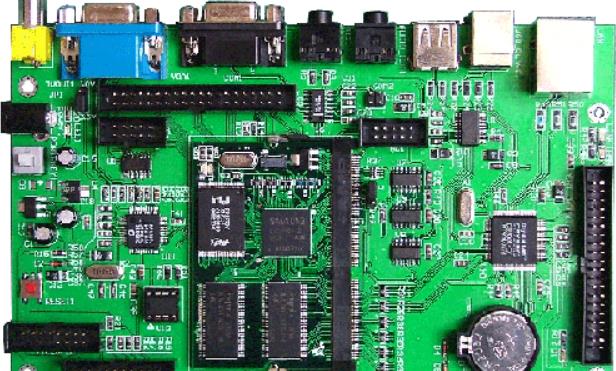
Grounding and voltage wiring in PCB design
Key points:
·Understand the layout and design of the jumper grounding and voltage wiring printed circuit board
·The Best Practice of Realizing Power Supply and Ground Plane in PCB Design
It's easy to plug the power cord into a wall outlet or turn on the light switch. You may think that it is also easy to connect the components on the printed circuit board to the power supply or ground. To be honest, PCB design used to be like this. On circuit boards where signal and power integrity are not important, you can place vias in the power or ground plane and ignore them.
However, according to the design requirements of today's electronic products, there are many things to manage the distribution network, not just to add some vias in the design. You need to consider the impact of PDN on the rest of the circuit board, and ensure that the equipment can use the appropriate power supply and grounding grid. This requires some skills in circuit board grounding and voltage wiring, and we provide some useful ideas here.
Grounding and voltage wiring on the printed circuit board
Circuit board
Although today's dense multilayer boards are widely used in advanced electronic equipment, cheap double-layer boards are still needed. For equipment that does not require many circuits (such as toys or other simple consumer goods), double-layer boards are still preferred to reduce manufacturing time and cost. However, at the same time, the efficiency of these electronic devices is still improving, which requires more efforts in the power network design of circuit boards.
Only two layers are needed when using, and there is no available internal layer for power supply and ground plane, so the power supply must be wired. It is recommended that in most applications, designers use the smallest possible track width and can still manufacture at a lower price. This usually results in 6 million channels of signal and 20 million channels of power. Remember that the power trace width is proportional to the current. If the current increases, the trace width will increase, and vice versa.
When wiring, the signal and power wiring should be placed on the top layer, and the return path should be kept on the bottom layer. The simplest way is to dedicate the ground floor as a solid ground plane. You may end up having to use some of the underlying layers for signal routing, but if you want to ensure that you keep a clear path for signal returns.
Routing voltage and signal routing need to be carefully planned
Using bottom grounding can also help you solve noise and other signal integrity problems, but it can also take up a lot of space. This is very important to carefully plan the top-level power wiring to ensure that the power is evenly distributed on the entire circuit board.
If the SMT pin is connected to a power supply or ground with a large area of metal, it may cause a thermal imbalance between the SMT pin and the pin with less metal. In smaller discrete parts with two legs, this imbalance can lead to a situation called "tombstone impact.". This is the place where the reflow speed of solder on one pin is faster than that of the other pin, and the part is pulled away from the other pin.
When connecting discrete SMT pins to ground or voltage wiring, it is best to use a track width that is wide enough to meet current requirements to provide heat dissipation. This will help to maintain thermal balance between the two pins of the device.
Another problem with small discrete parts is placing pins on large areas of metal Although this provides the best power efficiency, it also acts as a huge radiator, generating a large thermal imbalance with another pin To meet the requirements of power design and PCB manufacturing, connect SMT pins to multiple traces or "connect". "This provides the heat dissipation required for soldering to SMT pins
Through hole pin:
The connection between the through hole pin and the power and ground traces is usually the same as any other trace, and it needs to be directly connected to the pad of the pin from the trace. If the track is wider than the pad, or there is a metal filled area (such as power supply or ground plane), you need to use a thermal pad, as shown in the following figure.
These radiators can provide enough metal to conduct current, but reduce the heat absorbed by the metal plane from the pins. With PCB design tools such as Cadence Allegro, you can control the width of cable ties and the spacing in thermal pads to provide enough metal for pads to meet their needs.
Radiator with through-hole pin in the ground plane
Advantages and disadvantages of power supply and ground plane
If you are designing multilayer boards, you may need to include a board stack for dedicated power and ground planes. The biggest advantage of using aircraft is that it provides a simple way to connect components to the power supply and ground without the need for wide tracks and wiring as on a two-layer board. There are many other benefits to using ground planes in your design, including:
·Return path: the signal will be transmitted from the source to the destination, and then it needs to return to the source. If there is no clear return path, they will generate a lot of noise when hovering, which may affect other circuits. The ground plane will provide this simple return path.
·Masking: The ground plane will help shield sensitive circuits from external electromagnetic interference (EMI), and prevent internal EMI from affecting other equipment. In addition, the use of ground planes between active signal layers in the design will help reduce the possibility of lateral coupling or crosstalk between layers.
·Noise reduction: when the digital circuit is switched, it will generate noise pulse through the grounding circuit, which may lead to wrong switching in other circuits. The large area of the ground plate will help to reduce the impact because its impedance is lower than that of the ground wire passing through the track.
·Heat dissipation: The ground surface also provides a good radiator for hot components. By connecting these components with holes to the ground plane through the circuit board, the heat can be evenly distributed on the circuit board.
·On the other hand, some disadvantages should be noted when using power supply and ground plane. This plane will increase the number of layers of the circuit board, which will increase the manufacturing cost. Different areas of a circuit (such as digital and analog) need to carefully manage their grounding so that noise from one circuit does not adversely affect the other. Moreover, great care must be taken when using a split aircraft to accommodate multiple power supplies or grounding grids. This is particularly important for the signal return path, because the separation surface may inadvertently destroy or block the path that should be unobstructed.
However, all these problems are PCB design processes, and advanced PCB design tools can skillfully solve these problems