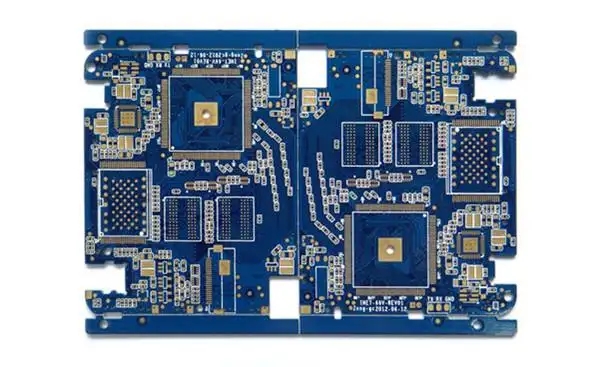
PCB factory explains the basic knowledge of PCB ink
PCB manufacturing, PCB design and PCBA processing manufacturers explain to you: PCB manufacturers explain the basic knowledge of PCB ink
PCB ink characteristics
01
Viscosity and thixotropy
In the process of PCB manufacturing, screen printing is one of the indispensable important processes. In order to obtain the fidelity of image reproduction, the ink must have good viscosity and appropriate thixotropy. The so-called viscosity is the internal friction of liquid, which means the friction force exerted by the internal liquid when one layer of liquid slides on another layer of liquid under the action of external force. The mechanical resistance encountered by the inner layer sliding of thick liquid is larger than that of thinner liquid. The unit of viscosity measurement is poise. In particular, it should be noted that temperature has a significant effect on viscosity.
Thixotropy is a physical property of a liquid, that is, its viscosity drops when it is stirred, and then quickly recovers its original viscosity after it is left standing. By stirring, thixotropic action lasts for a long time, enough to make its internal structure reconstitute. To achieve high-quality screen printing effect, thixotropy of ink is very important. Especially in the process of scraper, the ink is stirred to make it liquid. This function speeds up the speed of ink passing through the mesh, and promotes the ink separated from the original mesh to be uniformly integrated. Once the scraper stops moving and the ink returns to the static state, its viscosity will quickly return to the original required data.
02
Fineness
Pigment and mineral filler are generally solid. After fine grinding, their particle size does not exceed 4/5 microns, and they form a homogenized flow state in solid form. Therefore, it is very important to require the ink to have a fine degree.
two
Precautions for using PCB ink
According to the practical experience of most manufacturers in using ink, the following provisions must be followed when using ink:
1. In any case, the temperature of the ink must be kept below 20-25 ℃, and the temperature change cannot be too large, otherwise the viscosity of the ink and the quality and effect of screen printing will be affected.
Especially when the ink is stored outdoors or at different temperatures, it must be put at the ambient temperature for several days before reuse or the ink bucket must reach the appropriate operating temperature. This is because the use of cold ink will cause screen printing failures, resulting in unnecessary trouble. Therefore, to maintain the quality of the ink, it is best to store it at or under the process conditions at room temperature.
2. Before use, the ink must be fully and carefully stirred manually or mechanically. If there is air in the ink, it should be allowed to stand for a period of time. If dilution is required, the mixture shall be fully mixed first, and then the viscosity shall be tested. The ink bucket must be sealed immediately after use. At the same time, never put the ink on the screen back into the ink bucket and mix it with the unused ink.
3. It is better to clean the screen with a suitable cleaning agent, which should be very thorough and clean. When cleaning again, it is better to use clean solvent.
4. The ink must be dried in a device with a good exhaust system.
5. Screen printing shall be carried out at the operation site where the operation conditions shall meet the technological requirements.
three
Common Problems and Countermeasures of PCB Ink
01
Ink unevenness
The printing ink on the board can not be uniformly attached to the dot strip or flake ink white spots (no ink)
·Insufficient ink mixing time
·Ink mixing error
·Residual oil stain or water stain on the board surface (unclean pre-treatment)
·Ink impurities (the surface tension is damaged due to the mixing of tape oil stains)
·Poor material of rubber scraper
·The screen is not clean
·Expired use after ink mixing
countermeasure
·Check the pretreatment line to confirm the operation quality of the drying section
·Check whether each section of pre-treatment meets the process standard (water break, abrasion mark)
·Confirm ink mixing parameters
·Clean the screen, replace the scraper and other tools
02
Large copper surface cavitation
(1) The ink on the large copper surface is separated from the copper surface in the full coverage area
·Poor pre-treatment
·Adhesion of impurities on the board surface
·Copper surface depression·
·Poor ink mixing
·Uneven ink thickness on copper surface
·The ink surface is damaged by impact
·Uneven oven temperature distribution and insufficient or excessive baking
·Multiple tin spraying or too high tin spraying temperature
countermeasure
·Check the pretreatment line to confirm whether each working section can meet the quality requirements
·Confirm baking temperature and oven distribution temperature rise curve
·Confirm ink mixing parameters
·Check the production process to reduce external impact
·Confirm tin spraying operation parameters and conditions
(2) Large copper surface or line surface corner ink full coverage area ink and copper surface separation
·Ink printing is too thin
·Poor pre-treatment at the corner of the line
·Insufficient baking
·Multiple tin spraying or too high tin spraying temperature
·Soak the flux too long
·Excessive attack power of flux
·Damaged ink at corners
countermeasure
·Adjust the thickness of solder mask printing
PCB manufacturing, PCB design and PCBA processing manufacturers will explain to you: PCB manufacturers will explain the basic knowledge of PCB ink.