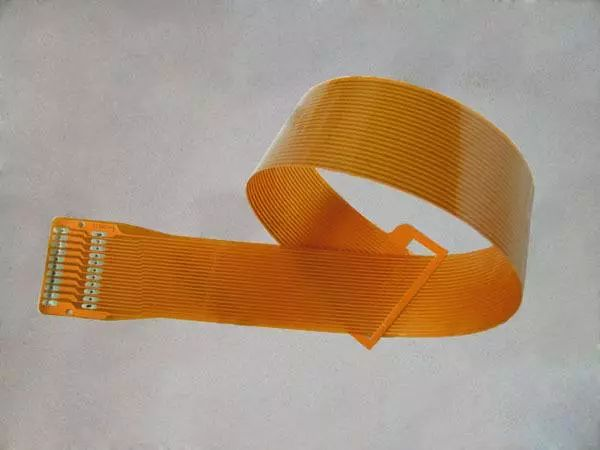
As the requirements for assembling components on FPC become more and more popular in the smart wearable industry, SMD surface mounting on FPC has become one of the development trends of SMT technology due to the limitation of assembly space. However, FPC is more difficult to assemble than PCB because it is not so sturdy. Today, let's understand the difference between assembling flexible plates and rigid plates.
1. Welding process
Like PCB process, solder paste is covered on FPC and soft and hard bonding plates through the operation of steel mesh and solder paste printer. However, the surface of FPC is not flat, so we need to use some fixing devices or add reinforcement to fix it. Usually, we will paste reinforcement in the component area of FPC.
2. SMT component placement
In the current trend of miniaturization of SMT components, small components will cause some problems during reflow soldering. If the FPC is small, elongation and wrinkles will not be a serious problem, which can reduce the SMT frame or increase the marking points. If you do not want the stiffeners glued to the bottom of the assembly, you may need flexibility after assembly. Therefore, SMT fixture will be a good choice.
3. Reflow soldering process
FPC must be dried before reflow soldering. This is an important difference between FPC and PCB assembly placement. In addition to the dimensional instability of flexible materials, they are also relatively hygroscopic. They absorb water like sponges. Once FPC absorbs moisture, reflow welding must be stopped. PCB has the same problem, but has higher tolerance. FPC needs to be preheated and baked at 225 ° - 250 °. This preheating and baking must be completed quickly within 1 hour. If it is not baked in time, it needs to be stored in a dry or nitrogen storage room.